These documents will provide a firm foundation for your system assessment. Continue to record each possible defect and solution as you find it throughout the inspection.
Hydronic system defects can include:
- Absence of flow control valves and test ports
- Undersized piping
- Excessive fittings
- Poor equipment installation
- Wiring and control defects
- Evidence of leakage and corrosion.
While you complete your inspection, create an ongoing list of repairs and upgrade recommendations you can offer your customers to improve system performance.
Start-up the System
Adjust the controls to call for the desired operating mode to start the system. Assure the system responds appropriately to each control change and note any corrections needed on your customer report.
Each flaw you find will lead you closer to the solution your customer wants. Listen to the system start and operate. Inspect and document unusual noise, vibrations, water hammering, or air sounds moving through the water system.
Find the Problem Yet?
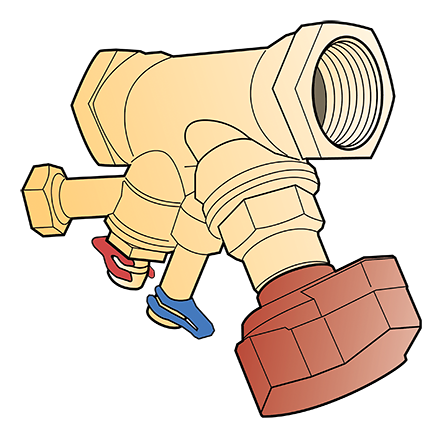
The problem is often revealed when you inspect the system, review equipment specifications, and start up the system. You’ll find many of these potential repairs during inspection:
- If there is air in the system, bleed it out through the bleed valve
- Plugged strainer (system filter)? Clean it
- If the pump speed is adjustable, make a note of it and adjust the pump speed accordingly
- Power or control issue? Correct it.
Temperature Testing
Since heating or cooling equipment transfers heat, temperature testing and diagnostics are essential on hydronic systems. The quality and accuracy of instruments such as temperature measurement pipe clamps are increasing while their cost decreases.
Measure the temperature on the pipe surface before and after the equipment. You can use these measurements to interpret water temperatures with reasonable accuracy. Subtract the two temperatures to find the temperature difference.
One word of caution; when testing and diagnosing hydronic system temperatures, understand they are affected by fluid flow volume and deficient equipment performance. When analyzing system temperatures, your evaluation must consider flow and equipment function as two separate causes of performance losses.
Compare the measured equipment temperature change to the manufacturer-listed temperature change range. Typically, if the temperature change is low, it is evidence of either high fluid flow or poor equipment performance.
Should the temperature change be mid-range, this may indicate the system’s flow and performance are acceptable.
When the temperature change over equipment is high, it may be good evidence of low fluid flow.
Click Below for the Next Page:
Recent Comments