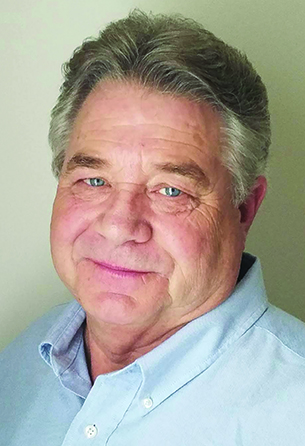
John Puryear
Sometimes our industry spends more time focused on equipment than on how to deliver comfort into living spaces efficiently. This article details a common rule-of-thumb based on the physics of air movement in a duct system that has all but been forgotten.
“We Have Always Done It This Way”
Most HVAC contractors, depending on their geographical location, have a standard duct system type they use when installing equipment — usually during the initial new construction phase. Currently, local jurisdictions may require a Manual J, Building Heat Loss/Heat Gain calculation, and sometimes a Manual D, Duct System Design drawing. This development was not common 20 years ago.
Many contractors assume the duct system is sized and installed correctly according to the local code. They also assume that the HVAC equipment is producing and delivering the “correct amount of air” to the duct system. This assumption can lead to ductwork going untouched for decades. Then, when a contractor is confronted with an airflow issue by the customer, he takes out his trusty Handometer, holds it over the register in question and agrees with the customer.
Then he says something like, ‘All we have to do is add another outlet in this room or maybe a return. If that doesn’t do it, we’ll increase the fan speed if possible.’
Don’t laugh, a lot of us are guilty of having done this – even me.
What Most Customers Believe
Typically, customers believe comfort/air issues are an equipment problem. The customer calls a contractor and tells the customer service representative, ‘I’m thinking about replacing my HVAC system, when can you come over?’ A comfort advisor shows up promptly and the homeowner says,’ I was talking to my neighbor and they had a bigger unit installed. I think I need a bigger unit!?
The truth is, until the system is examined and tested, no one has any idea what the problem might be. Performance-Based Contractors’ are trained to verify equipment is sized correctly for the home and conduct static pressure tests to show customers that oftentimes the equipment isn’t the culprit. In fact, it is often the duct system attached to the equipment that is causing the problem.
Poor Airflow Is Common
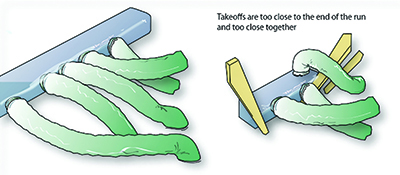
Two common ductwork installations
Unfortunately, we as contractors have trained customers over the years to accept poor airflow. Rooms over garages and bonus rooms are usually the worst, but the upstairs in a two-story house is typically five to 10’F higher than the first floor. Installing contractors usually lack knowledge about airflow, don’t have a room-by-room Manual J and/or D, or they use too many rules-of-thumb in duct design. They also most likely never used any airflow testing protocols like NCI’s AirMaxx’ app, Air Upgrade Worksheet, or ComfortMaxx Verify’ software. This leads to what happens next.
What Causes the Airflow Issue?
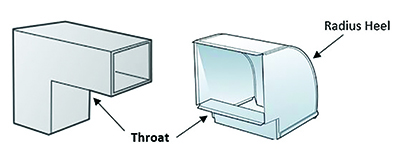
These two elbows shown above have the same restrictive throat even though one has a radius heel.
A common airflow problem comes from high static pressure in the ductwork which causes ‘turbulence.’ Turbulence is the physics of airflow that shows how air rolls and tumbles through the duct, almost like a ‘corkscrew.’
The combination of air rubbing against the wall of the duct (resistance) and turbulence in the air stream itself creates friction loss. This friction loss shows up in poorly designed duct fittings because transitions are too short or because of square-throated elbows.
How Do We Fix This? The Two-Foot Rule
The air from the supply side converts from velocity pressure to static pressure so it can disperse into the branch runs. This turbulent flow pushes against the sides of the duct and creates static pressure. Whenever there is a directional change in airflow, from either an elbow, transition, take-off, etc., it takes 18 to 24 inches from that airflow change to ‘re-pressurize’ the duct and resume the turbulent air movement.
This pressurized air then comes upon a take-off for a branch runout. The air escapes down the branch and the turbulent flow stops and smooths out. Technically this means it loses some pressure. The air now has to re-pressurize to regain its turbulent flow so it can continue to push its way down the duct. It requires about 24′ or two feet to do this. This is the ‘Two-Foot Rule?.
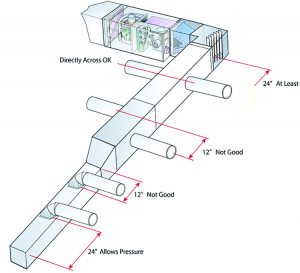
Ideally, you should allow at least 24′ between takeoffs and at the end of any duct run.
When asked, ‘which is better, to put take-offs directly across from each other or to stagger them,’ most students say to stagger them. This is correct if the stagger is 18 to 24′ on center from each other. Look at the diagram.
If you place take-offs too close together, less than 24′ on center, or too close to an air change (elbow or transition), the air doesn’t have time to re-pressurize and create the appropriate turbulent flow.
Where Do You Put the Last Take-Off in The Trunk Duct?
It is safe to say that most installers know to never put an outlet in the end cap of a duct system. So where do you put it? Two feet from the end. There are two ways to address this issue in duct renovation. You can move the take-off upstream by 24′ which is labor intensive. The second way is to remove the end cap and add 2 feet of duct and re-attach the endcap. This is usually simpler. You have to decide which is more cost effective.
Making It Happen
The type of installation common to your area may not accommodate this rule. If you have a system with remote plenums or an extended plenum that is 6 foot or less with multiple branch runs, this rule may not work. NCI suggests that the installer use NCI’s Duct Design Tables, NCI’s Guide to Enhanced Duct Installation Practices, and your company’s duct installation procedure to fix the problem.
The goal of this article is to raise your awareness of turbulence in the ductwork and how it affects air delivery through restrictive duct fittings. It’s also to show how spacing takeoffs for branch runs using the Two-Foot Rule will relieve unnecessary pressure on the fan.
Customers want to be comfortable and do not understand our technical terminology and testing processes. Our job is to give them options based on testing and reviewing the system. Using the “Two-Foot Rule’ on your next project will lead to greater customer satisfaction and a sense of pride of a job well done.
John Puryear has a background in duct design, sheet metal fabrication, and installation in both commercial and residential HVAC. He currently serves the industry as an instructor for the National Comfort Institute (NCI). If you’re a contractor or technician wanting to learn more about duct airflow, design, or renovation, contact John at johnp@ncihvac.com or call 800-633-7058.
Thank you for breaking down the common causes of airflow issues! This is super informative and really helped me understand what might be going wrong with my system. I appreciate the practical tips for troubleshooting—definitely going to check these out!
Does the two-ft. run have to be a straight shot after? Could you say come to the end of a run where you want your vent and turn 90 degrees vertical for the final two feet and have the vent after the elbow? This would be like an “L” on its side.
Likewise, rather than having two vents branched directly across, can you make a “J” horizontal and the last two feet fulfilling the two-foot rule as well?
Jamez, These are excellent thoughts for further review. Experience with testing will help determine what is the best avenue to consider. Remember that the “2 foot rule” is physics and “Air” has a mind of its own.
To answer your questions, consider this:
Q1. Straight shot – Yes and No. Yes in the fact that it takes 18 to 24 inches to achieve proper pressure in the duct for airflow. No, if you are going to put the takeoff less than 2 ft. before or after elbow.
When you say, “when you come to the end of a run,” do you mean the end of a trunk run or branch run? There is a difference.
I am a bit confused about what you are asking. You may reach me through my NCI email, for an immediate response and/or attend a Duct System Optimization class near you.
ACCA Manual D 2016 3rd Edition Version 2.50 in Section 5:5-6, 5-7, 5-8 discusses end of trunk takeoffs/registers.
Hi John, great article. If joists run perpendicular to the trunk and the trunk terminates at the basement wall, how do you adhere to the 2 ft end cap guidance? My outside wall is parallel to the joists and there are two registers on that wall. They are supplied by two separate takeoffs directly at the end cap. I may be able to takeoff further upstream of the end cap and run them parallel to the trunk before turning into the last joist bay (2 90deg turns). Or, takeoff at 90 in an earlier and then 180 to navigate underneath the joists. Alternatively, can the trunk be extended downward at the wall to provide the final 2ft?
Thoughts?
Thanks,
Darrel
Thank you for the inquiry. You are correct. Without getting into too much detail, I recently had a homeowner with the same issue that had read the article, contacted his HVAC contractor who told him it wasn’t necessary. He insisted to no avail. He went to Lowe’s, got the materials, installed them himself, and said that by adding a round off-the shelf elbow (appropriate size) and 4 feet of pipe with end cap gave him the additional airflow the room was needing. Using the 2-Foot Rule, he re-attached his branch runs and said there was a huge improvement in the air in the room. THe most comfortable it had ever been. The gentleman sent before and after pictures.
The only thing I need to reminder you is if you are using rectangular duct, please install a 90 degree elbow with single-wall turning vanes to accomplish the same effect.
This article provides valuable insights into the ‘two-foot rule’ for effective HVAC installation. The rule makes sense in ensuring proper airflow and performance. It’s crucial to consider factors like obstructions and ventilation when placing HVAC components. This rule can contribute to better system efficiency and comfort for homeowners. https://www.redsealcomfort.com/
John,
Is there an NCI standard or manual (or other organization) that drives the Two-Foot rule or is this mainly industry best practice?
I am concerned that if I confront my designer/installer on complying with this, he’ll just say “Nah, we always do it our way and that works.”
Peter, this is an NCI and the HVAC industry best practices standard (NCI calls it High-Performance HVAC Contracting). But let’s talk about the contractor who says, “Our way works. We don’t ever get any complaints.” My next question would be, “Then I guess you have an Airflow Capture Hood (Balancing Hood) calibrated to NIST Standards, and you can provide me with a final airflow report for each room?”
This information protects you from the contractor who doesn’t Test-In or Test-Out or use best practices.
You asked the $64,000 question.
What was not put in the article was how this came about. When I started (before there was water, lol) in 1973, one of the grizzled ol’ mechanics I worked for taught me this. Being young and dumb, I asked him, “Why?” He said his mechanic told him, and he said it always worked.
Well, I took that as “It is because it is!” As I grew in the industry and learned to test, I discovered it was true. I am not the brightest bulb in the pack, so I searched for the origin. If it’s physics, it had to be written somewhere.
I spent years reviewing the Duct Design manuals, ASHRAE, SMACNA, and ACCA. I asked engineers (the ones that would talk to me) to no avail. The physics work because “air” has a mind of its own. You have to tell it what to do! It is a fluid, and there are laws that it must adhere to.
Remember: There are three basic Air laws: a) It will follow the path of least resistance, b) 1 cubic foot of air per minute (cfm) IN equals 1 Cfm OUT, c) the highest pressure is always where it is generated from (usually a fan).
I will give a nod to the ACCA Manual D Duct Design manual. It states in Manual D Third edition, v2.50, 2016 printing in Section 5, pages 30-31, Paragraphs 5-6 and 5-7, that there needs to be a minimum of 18 inches at the end of a trunk duct.
Now that I have that off my chest, I thank you for the inquiry, and I trust I didn’t ruffle any feathers. If I can be of service, you can reach me directly at johnp@ncihvac.com
Great article! In the diagram, it shows two takeoffs directly across from one another as being ok. Does the same hold true if the takeoffs are located 90 degrees from one another? Think a top take off and a side take off.
Dan, great question, back at ya! Yes and No! Way to be decisive, right?
Anyway, there are a couple of things to consider. First, having the “air break” inline with each other is better. That’s the “yes” part.
Secondly, the other consideration is how air travels down a rectangular trunk line. In rectangular duct, the highest air pressure is on the sides of rectangular ducts with the top next, and the least pressure is on the bottom. In other words, the highest pressure is exerted on the sides, next highest pressure is the top, with the least pressure at the bottom.
Referring to the diagram, you’ll notice we depicted “top” takeoffs further down the air stream. These takeoffs are always recommended when installing on the top. NCI never recommends same size takeoffs for the branch runs. Top takeoffs because of the elongated rectangular size to round size allows for more initial airflow into the branch run.
If you use side round airtite takeoffs (RATs), make sure that they are at least 1-in. bigger than the branch run size. When using these two types of takeoffs “with manual air volume dampers,” they will always yield “controllable” air to the register.
We discuss this scenario during our Duct System Optimization class. You may want to attend for a better understanding.
If you would like a more detailed answer, email me direct at johnp@ncihvac.com. I trust this helps.
Great article explaining ways to improve duct performance. I was wondering if you had any experience with double top takeoffs when directly across branch runs are needed, but there is no room for side takeoffs? Do these work well or become a pinch point in the airflow?
Andrew, double top takeoffs, in the scenario you described, are common when installing them in the joist bays of a basement soffit. This is usually done because of space and airflow into the Air Mixing space in the room of the above floor. In some cases one takeoff connects to the basement register and the other connects to the above floor.
The next thought is what kind of takeoff are you using? Dovetailed Elbows? Tab collars and elbows? Flat airtight takeoffs and elbows? Or are you using a true Adjustable Elbow Top Takeoff (which is preferred)?
The elbow takeoff at the trunk connection has a round diameter width by diameter width + 1.5 inches. Example: the base of a six-inch adjustable elbow top takeoff has a base size of 6 in. X 7.5 in. with airtight gaskets or bendable tabs. This allows for the air to pass with less restriction into the branch run.
You mentioned pinch points. The “Equivalent Length” of a conventional same size takeoff as branch run connection to rectangular trunk is 35 feet. For a round pipe connection, it is 50 feet. If you use a Top Takeoff as described above or enlarge your tab collar or airtight by 1 to 2 inches and then reduce, you now have an “Effective Length” of 10 feet. This is a substantial decrease in static pressure/blood pressure of the duct system.
In all scenarios, remember to add air volume control dampers in all takeoffs for air balancing.
NOTE: The physics of residential system air traveling in a rectangular trunk, is pressurized, not velocity-driven. The greatest pressure is on the sides of the trunk system, the top is next, and the bottom is least. Side takeoffs are preferred.
We discuss this scenario during our Duct System Optimization class. You may want to attend for a better understanding.
If you would like a more detailed answer, email me direct at johnp@ncihvac.com. I trust this helps.
I was wondering if a straight 40’ unit on one end of run is OK to do all in one size or do you think a reducer is needed somewhere down the line?
Scott, Manual D (Duct Design Manual) recommends that to keep the pressure in the trunk line “stable,” you must maintain one size of duct for 24 feet and then reduce. So in your description, about halfway down you need to reduce the size to accommodate the airflow drop based on how much air (cfm) you have used in the first half of the trunk duct.
Example: Trunk starts at 16-in. metal round pipe (from NCI’s Duct Design Table for Round Metal pipe) and handles 1200 cfm. It has 4 to 7-in. flexible duct branch run-outs handling 110 cfm (again based on NCI’s Flexible Duct Design Table) which equals 440 cfm total.
Subtract 440 from 1200 cfm (main trunk) that equals 760 cfm which translates to a 14-in. round metal pipe that handles 770 cfm (NCI Duct Design Table) at 20 feet downstream.
This is a pretty simple solution. There are other factors that may suggest another reduction but that is a discussion for another time. We discuss this scenario during our Duct System Optimization class. You may want to attend for a better understanding.
If you would like a more detailed answer, email me direct @ johnp@ncihvac.com. I trust this helps.
Underlying issues in your duct system can lead to a number of problems relating to the comfort and safety of your family. A duct system analysis is designed to uncover these issues and provide you with a thorough analysis prior to completing any repairs. Once the technician has examined your duct network, they will present you with their findings and provide recommendations for any work that needs to be done.
Hello John,
Outstanding article and concept in Two Foot-Rule. As soon as I read this, I had to go up in the unconditioned attic to measure the takeoffs.
The results are:
— Straight plenum larger trunk length 4′ 10″ / 58″ inches with 1 smaller transition trunk length 7′ 8′ / 92″ inches, 6 total branch side takeoffs (90 degree), 3 branch takeoffs located on each side
— Larger trunk has 2 left side takeoffs (1 & 3), and 1 right side takeoff (2)
— Smaller trunk has 1 left side takeoff (6), 2 side right takeoffs (4 & 5)
— Each branch takeoff is numbered sequentially based on closet distance from air handler, 1 = closest, 6 = farthest
— 1, 2, 3, 5 takeoffs are 7″ inches in diameter, 4 takeoff is 5″ inches in diameter, 6 takeoff is 8″ inches in diameter
— 1 left = 18″ inches on center from air handler
— 2 right = 28″ inches on center from air handler, 10.5″ inches on center diagonally across from 1 left takeoff, 12.5 ” inches on center diagonally from 3 left
— 3 left = 17.5″ inches on center before plenum transition, 22.5″ inches on center from 1 left takeoff, side by side
— 4 right = 21″ inches on center after plenum transition
— 5 right = 13″ inches on center from plenum transition end cap, 2.5″ inches on center diagonally across from 6 left
— 6 left = 10.5″ inches on center from plenum transition end cap
Based on your HVAC duct takeoff Two Foot-Rule, it looks like I may be a candidate for adding additional duct to extend the end cap. Also should I consider moving 2 right takeoff closer towards the air handler and at same time better alignment across from takeoff 1 left. I trust 1 left takeoff 18″ inches on center is acceptable distance from air handler.
Would you agree with these solutions?
I also have a return air box that is separated from the return plenum but connected with a 16″ inch diameter metal flex duct. The return box round opening takeoff is horizontal to the ceiling and the return plenum round takeoff is also horizontal to the ceiling. Unfortunately each 16″ inch opening is neither vertically or horizontally in alignment. Picture a 16″ inch flex duct slinky attachment.
Based on your HVAC takeoff Two Foot-Rule comments section, it looks like I may also be a candidate for moving the return plenum takeoff from the top to the side, in the center of the end cap.
Would you agree with this solution?
Thank You in advance for your response.
Patrick, “By Jove, I think he’s got it!” (excuse me, really old reference)
Yes, you understand the principle and your solutions are correct. The return may be an issue, though. The Air Diffusion Council (the authority on flexible duct installation), suggests to always make the “flex” straight with an inner core pulled tight. NCI Best Practices suggests to use metal 90 degree elbows the same diameter as the flex if you need to turn the flex.
I would caution you before you make the changes. Based on the NCI Duct Design Tables, with your current amount of outlets and their sizes that you gave me, your total cfm is 650 cfm, 4 – 7″ = 440 cfm, 1 – 5″ = 50, 1 – 8″ = 160.
If this is the total number of outlets, I would be curious to know the size of the installed HVAC system. Traditionally, 6 branch run-outs would indicate a 1.5 ton HVAC system which handles 600 cfm. The condenser (outdoor unit) would have 018 in the model number. If the condenser has a 024 in the model number, this would be a 2-ton system which equals 800 cfm. As you can see this shows you are 150 cfm short on the necessary airflow.
I am a DIY guy myself but when it comes to the trades, a professional should be considered. NCI has a Consumer website: http://www.MyHomeComfort.org, where you can find a Certified NCI Performance Based Contractor near you.
The article shows my email address if you need further assistance or to find someone near you.
From what I’m reading, can I conclude that a 48′ PLENUM can have only one duct run out of it?
In a horizontal situation I need 24 inches after the coil before my first takeoff. Then each takeoff needs 18″ and then another 24″ at the end. If I have 8 branch runs that is 8 X 18″ + 2′ + 2′ which is equivalent to 16 feet of plenum.
I’ve never seen that much plenum or ducts spaced that far apart. The installations we do seem to work fine. No call backs or complaints. Thoughts?
Glenn, that’s a great question, just not quite the right interpretation. Let me see if I can clarify.
I assume if you are using plenums directly on the equipment, you need more than one trunk branch to feed multiple outlets. The 2 Ft. Rule is just a guide to help alleviate static pressure at the fan.
An NCI member in Texas has been testing their systems designed that way and has discovered that by adding two more feet to the four-ft. plenum, the TESP (Total External Static Pressure) of the system is reduced by 40%. This type of system design is called an “Extended Plenum” system. I have pictures and would like to discuss this further with you. You can reach me at johnp@ncihvac.com.
It is a little more involved than our discussion here so email me directly. Question: Have you tested and balanced the systems you installed to see if they are producing the required airflow to the rooms that they are attached to? NCI has found that in many cases there was improvement but the system was still not delivering the required amount of airflow to the living space.
Not having call backs does not necessarily mean the system performs well. If you are a performance-oriented installer you will make sure you test your system against the manufacturer’s specifications. That is the only way you deliver the capacity and efficiency promised to your client.
Good article and understandable from a layperson’s view. I feel like I want to take pictures of my current system and analyze (or have someone analyze) current airflow issues in my home. I think I am the 4th owner of this 1949 bungalow that has has several additions added to it. Only after living in the space and putting up with all of the quirks have I come to the conclusion that I need to be more proactive in remedying the status of my home.
I have already determined that the additions were done ‘on a shoestring‘ and not properly constructed. Probably not even inspected, I suspect. Just this morning I have found at least four apparent issues with the HVAC supply and return setup.
I can’t wait until early spring so that I can get moving forward with a lot more knowledge from professionals like you helping the homeowners. THANKS!
Thanks for your comments. Please bear in mind that it takes a professionally trained and certified contractor to track down and fix airflow issues in your home. My suggestion is that you find one as close to your local area as possible. Just go to our locator page here: find-a-contractor.
Great article. I purchased a new build in Montana were the HVAC contractor installed four take-offs within the two-foot end space on one zone; and three take-offs within the two-foot end space on another zone. I had no airflow in these two zones from the registers.
I extended the supply duct on both zones to give me the two feet needed and it made all the difference. I now have airflow! Thanks
If your trunk line isn’t long enough to place all your takeoffs with proper spacing, are you better off using one less takeoff in a large room or sacrificing the spacing? Large room 12×24 w/8” takeoff but straight off the trunk without flex?
Seth, that is a great question.
As you know, we don’t recommend branch runs directly out of the endcap of a trunkline.
My first suggestion is to extend the trunkline by two feet, then move and enlarge the takeoff with a damper by two inches of the new branch size. That will accommodate the required airflow for the occupied space.
Place the new takeoff on the side of the duct, two feet away from the endcap. If you cannot add the two feet of duct, follow the takeoff enlarging with the damper process previously mentioned.
Supply register size, type, and placement are crucial in a large room. Please test and verify airflow upon completion of the correction.
If you need more help, refer to the article. My contact info is there.
Such a great article John. I’m amazed by this information. Commercial HVAC Spokane
Well explained John. I didn’t know if this at all. Quick question, Can I have a take off just before transition starts ?
If the takeoff follows the 2 ft. rule when installed, you should be OK. My rule of thumb is 18 inches on center before the transition. The actual rule says “24 inches on center,” not edge to edge of hole cutouts. I do suggest Pressure Profile Testing to verify that the installation is acceptable.
Good Rule to follow
Thanks for the clarification
John,
Does the two foot rule also apply from the place where the supply reducer is attached towards back to main supply?
Thanks
Vikas, I believe I just answered that in the previous inquiry. If you missed it or can’t see it, here is what I wrote:
“If the takeoff follows the 2 ft. rule when installed, you should be OK. My rule of thumb is 18 inches on center before the transition. The actual rule says “24 inches on center,” not edge to edge of hole cutouts. I do suggest Pressure Profile Testing to verify that the installation is acceptable.
I believe you said, “reducer” and I used the word “transition” but they are the same component.
Nice article. Can I have a hole at the end of the return trunk? I know it’s not recommended in the supply case. But I am not sure about the return case.
Great question! Here’s one back at you. Do we push or pull air into the Return? Supply ducts pressurize and discharge air through the supply registers. That discharged air then pressurizes the space and since the return side of the fan is basically creating a vacuum, that pressurized supply air is PUSHED into any available opening, usually an undersized return. Remember the old analogy of trying to push an elephant through a keyhole.
The simple answer to your question would be “Yes.” Just remember that since the air is “pushed” into the return cavity the most direct avenue of entry would be preferred. Make sure the return is large enough to accommodate the airflow and place the takeoff in the center of the end cap.
Thanks
Can you have three take offs in the same location as long as they are two ft from the end?
Thanks for the information in the article above.
Roger
Roger, I just saw this and don’t remember responding to it, my apologies.
Do you mean one on each side and one on top? If that is the case, not a scenario I would be fond of. That should decrease the static pressure overall but with three takeoffs so close, it would be a “crap shoot” on what the air would do.
Of course, try it and re-test to see what happens. Check static pressure, component pressure drop, and airflow with a balancing hood.
More information is needed (plus pics would be helpful) to further evaluate your question.
Thanks John. Great article and greatly needed.
Thanks for the kind words, Tom.