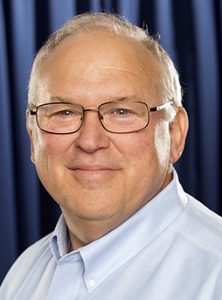
Rob Falke
How would it change conversations with your customers when you prove that one-third to one-half of their heating or cooling is lost by their poorly operating duct system? Would that spark their interest in you eliminating that problem?
Savvy HVAC contractors are finding practical ways to reduce duct system heating and cooling losses through testing, diagnostics, and making simple repairs to the HVAC systems they install and service. Customers are eager to purchase these repairs when they understand the cost of their duct system heating and cooling losses through live field testing and a simple calculation they participate in.
For example, home performance contractors typically prescribe replacing windows, appliances, shower heads, and light bulbs to save energy. This isn’t very appealing work to most HVAC contractors. But reducing the building load up to 50% by improving the duct system, and proving it to homeowners is right up our alley.
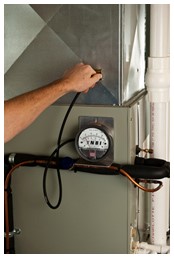
Measuring static pressure on residential HVAC systems helps you find whether duct leakage is hindering system efficiency.
Find Duct System Losses
Without diagnostic testing, load calculation software normally assumes a Btu loss of about 15%. Under peak summer and winter weather conditions this assumption will miscalculate actual losses by more than 300%. Especially during the peak heating or cooling days of the year when delivered system capacity is critical to comfort and impacts their utility bill the most.
So, to identify actual operating conditions, do a field diagnostic test on a live system to reveal defects you can correct. Without identifying and correcting these operating system defects, there is no way to control the load of a building or deliver maximum HVAC system performance.
Duct Leakage
Duct leakage is a real threat to the load of a building. You can reduce it in almost every situation. Btus lost or gained through leaky duct systems directly add to building load. This is especially true on the return side of the system. By tightening up a duct system correctly, you will reduce duct system heating or cooling losses.
But you can’t just slap mastic on the ducts and guarantee energy savings. When you know the average residential .50′ w.c. fan currently operates at over .80′ w.c. of actual total external static pressure, you must add more duct capacity to the system before duct sealing. Otherwise the result will substantially increase static pressure which then results in lower airflow and reduced system capacity.
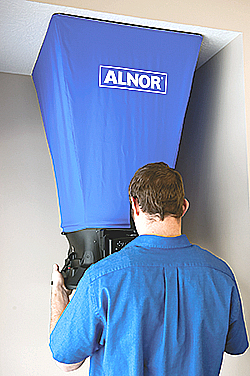
Using a flowhood, HVAC technicians can accurately measure airflow at the grille.
How efficient is a 20 SEER system at 250 CFM per ton? Unfortunately, this is the typical result of many duct sealing jobs.
So, before duct sealing, measure total external static pressure. This evidence helps customers understand the need for additional duct capacity before sealing ducts to assure adequate airflow
Once you install more or larger ducts, seal the duct system to assure no loss of’ airflow and Btus from the system on the supply side or pulled into the system on the return side. This will have a substantial and immediate measurable improvement in delivered system heating or cooling capacity.
Measuring Duct Leakage
Its best to measure duct leakage live with your customers using basic air balancing test methods. Measure the fan airflow, then measure and total the airflow at the supply registers, and then at the return grilles.
Subtract the total airflow of the supply registers from the fan CFM to find live supply duct leakage. Then subtract the total airflow into the return grilles from the fan airflow to discover return duct leakage.
Example: The system fan airflow is measured at 1000 cfm. The total airflow through the supply registers is measured at 800 cfm; the difference is the supply duct leakage of 200 cfm.
On the other side of the fan, the air at the return grilles measures 700 cfm. 1000 cfm of fan airflow minus 700 cfm at the return grilles reveals 300 cfm of return duct leakage. Duct leakage of 200 cfm on the supply side and 300 cfm on the return side totals 500 cfm of live duct leakage.
If you have been using duct pressurization methods to test duct leakage, you will find a substantial difference between the two duct leakage numbers. While duct pressurization testing is more widely accepted, the duct leakage number it provides has never claimed to represent a live duct leakage cfm number. Compare the two methods for yourself.
Duct Temperature Loss
Under live operating conditions, nearly all duct systems lose some of the Btus generated by the equipment. The question is how much? The only real answer is found by measuring the actual duct losses of the system. This is a quick and simple test that will often blow your customer away.
On the supply side, measure the air temperature where it leaves the equipment. Next measure the air temperature leaving the farthest supply register. Subtract the two temperatures to find the temperature change through the system. Ideally the two temperatures should be almost the same.
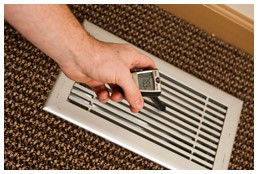
Measure air temperature at the register.
On the return side of the duct system, measure the return air temperature at the farthest return grille and subtract from the air temperature entering the equipment.
Measuring Air Temperature
The air temperature in the ducts should not change more than a degree or two. An air temperature change greater than this is evidence of a loss in system heating or cooling capacity. This loss is invisible and unaccounted for by most designers and service technicians.
Example: The air entering the return grille is 70?. The return duct passes through an attic at 40?. The temperature entering the equipment is 60?. Subtract 60′ from 70′ to find 10 degrees are lost through the return duct system from duct leakage and thermal loss.
To find the percent of Btu loss, divide the degrees of duct temperature loss into the temperature rise of the equipment.
Example: If the equipment temperature rise is 40′ and the duct temperature loss is 20′ then 20′ divided by 40′ equals 50% of the equipment generated heating Btus lost through the duct system. If the equipment output is 60,000 BTUs, multiply by 50% to find 30,000 BTUs of duct loss.
Doesn’t this turn 90% AFUE equipment into a 45% AFUE system? Your competitors can’t fix this system defect, because they are unaware the problem exists without measuring it.
Opportunity Abounds
This is only one example of new opportunities available to Performance-Based Contractors?. It is becoming more and more evident that those who educate their customers deliver better performing and more efficient systems. Using test and diagnostics while serving your customers will give you a substantial advantage in every sales situation.
Trackbacks/Pingbacks