In 2015, my wife and I were fortunate enough to buy the company where I was employed for five years. From a training and certification standpoint, the company, Masterworks Mechanical of Craig, CO had already taken steps with National Comfort Institute (NCI) to certify our field staff in combustion and carbon monoxide safety. As part of those initial steps, I attended my first training class taught by NCI’s Jim Davis in our hometown.
At the time I had 20+ years of experience in the HVAC trade. After the first day of class, my wife asked how it was. My answer: ‘They found the craziest guy in the nation and had him teaching about carbon monoxide (CO)!?
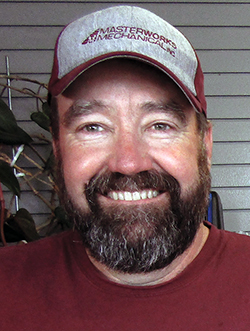
The second day, Jim proved all his knowledge to be true! The other side of this is that he proved I had spent 20+ years in the dark. I have since humbly apologized to Jim whenever I see him.
On the third day, he showed us how to put the practices he developed into play to provide safety for our customers.
His closing statement was that if we used what he had taught, we would be calling him to tell a success story about someone’s life we had saved. I felt like this was a pretty bold statement.
The Truth Will Set You Free
But then, 14 days after attending class, I did that very thing. I had used his training and our company’s tools to identify a boiler spilling CO to the point that the hallways in a two-story hotel were at 40 ppm.
Who knows how long this was happening?
With the onset of cold weather and the boiler running in longer cycles, (probably in the night) will CO form and harm someone? The point is, before my training I would have used a lighter in the draft hood to prove ‘the boiler was drafting well’ and went on my way.
This was when I realized how training provided the opportunity to identify life-threatening hazards on service calls. If I allowed shortcuts to move me to the next ‘no heat’ call, I may not get another chance to use my ability to prevent something terrible from happening.
The truth will set you free!
During the next few years, a contractor friend of mine, Tom Johnson, spent a lot of time explaining to me how his company does combustion tests on every service call.
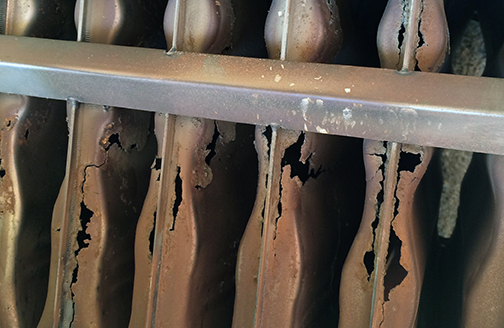
CO readings were insanely high!
Today this is more commonplace than not, but I had to visualize how it looked in practice before I could affect a change where there is no differentiation between what we do individually as technicians and collectively as a company.
What We Do Today
Today our company has 28 full-time employees, 19 of whom are field staff, and four are project/service, management staff. We service and install HVAC, Hydronics, plumbing, refrigeration, and water treatment systems.
Our team uses our ‘Combustion Safety‘ culture on every call. Up until the pandemic struck, each of our field techs held CO Certification, including apprentices. We’ll get back to this when travel becomes the norm once more.
Our success in doing this isn’t from our requiring it. It comes from assuring that everyone gets the chance to hear the stories firsthand from each teammate who saves the day for another customer. There is no better win, and everyone wants to be part of that.
Start a CO Safety Culture
Implementation starts with policy and procedure. I feel this is the easy part. You must first determine your commitment level.
Initially, I thought testing every unit we serviced was adequate. In discussions with Tom Johnson and the results coming in from the field, I discovered that many major safety events were being found in other equipment in the mechanical room in addition to the unit being repaired.
Our policy now is to combustion test every gas-burning appliance in sight. If we change a failed ignitor on a furnace, the water heater will be combustion and draft tested as well. Our plumbers test combustion on the water heaters they replace.
Each annual service agreement has a form for our techs to record combustion analysis for the customer’s gas-burning appliances. We keep track of these readings for five years.
The final thing our installers do after each replacement or installation of a gas-burning unit is to install an NSI low-level CO monitor (ncilink.com/NSI3000).
The number of times installing these monitors resulted in calls to identify issues that have made this our biggest gold star. The NSI 3000s are our companies’ night watchman.
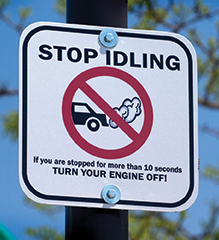
Advantages of the NSI 3000 CO Monitor
Here are two examples showing how this monitor helps identify and prevent life-threatening hazards like:
CO Infiltration from Attached Garages. We replaced a failed furnace in a house and was called the next day because their new monitor was alarming.
In troubleshooting the issue, we discovered car exhaust from the garage was leaking directly into the return air to the furnace through holes in the sheetrock ceiling and a poor seal in the return panning.
This caused CO symptoms in the family every winter for years.
Blockages from Snow. After installing a new tankless water heater, the new monitor we provided alarmed during mid-winter. During troubleshooting, we discovered that a pileup of snow had created a barrier.
This forced the condensing heating boiler to re-circulate combustion products into its combustion air.
The boiler was creating 2500 ppm of CO that was spilling into the room. The monitor indicated 35 ppm upstairs. It would have been much higher if this unit did not alarm at early levels.
After five years, I have an extensive list of examples just like these.
Click below for the next page:
Also along with the knowledge of mr Jim Davis if you ever have the chance to attend the heat exchanger experts class its a double whammy, that class was another amazing opportunity.
Jim Davis is the GOAT of carbon monoxide, NCI training, honestly anything that burns fuel of any type… I had the pleasure of installing his new HVAC system, and the knowledge that man holds is mind blowing. ( just don’t get him started on how much the women love his hair lol)
He’s a legend in our industry and an all around great man.