CO Safety Culture Creation
High-Performance testing and diagnostics policies and procedures provide the scaffolding to build the culture. Your co-workers commit to do the heavy lifting by consistently performing those policies and procedures.
For Masterworks, implementation began with our service crew. When an individual finds a CO-related problem, we discuss it during the morning meeting — explaining the call, talking about why and how they found the issue, and how to correct it.
One of our practices is in cases where we ‘Red Tag’ a unit. If we replaced it, we bring the old unit back to the shop.
We remove the heat exchanger from the red-tagged furnace and prove to all staff the validity of the tag. This builds confidence in the techs that when their analyzers and tools indicate a problem, the problem usually exists.
We spend a lot of time talking about the fact that in a 100-mile radius from our shop, there are nearly no other companies with staff who are trained and certified to do this. Your staff is how you successfully demonstrate your commitment to the community.
I would offer a few examples of what a Carbon Monoxide safety culture has provided us:
- One of our newer maintenance techs was able to save a person’s life by listening to staff reports of CO and how we address those issues.
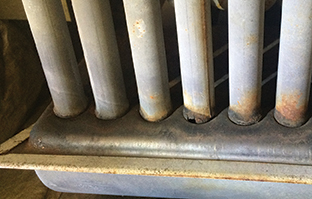
This technician was having a conversation with our dispatcher at the end of the day and she mentioned she had felt poorly since the weather turned cold. She had just been tested to see if she was anemic. Her headaches intensified at night.
The tech just had a feeling about what she said and gave her a ‘loaner’ low-level monitor for that night.
The next day in the office the dispatcher told him the alarm, which was placed on the nightstand where he had told her to put it, went off the previous night at 114 ppm.
She shut down her furnace.
We went out to her house and found a huge breach in the heat exchanger. The breach allowed the blower fan to fill the exchanger with room air to the point where CO ‘pegged the analyzer’ and spilled over above the burners into the house.
- Our company developed a procedure to identify breached or cracked heat exchangers. The procedure is designed from several sources. Using a combustion analyzer, we determine if the blower fan affects the combustion when ‘on’ compared to when ‘off.’ Using this test, we found that new furnace models we sell did not always pass on startup.
The Community Impact
Our distributor has three staff members who are NCI CO/Combustion certified. After demonstrating our test to them, they arranged a meeting with the manufacturer to share this finding.
At the meeting, the manufacturer toured us through their production line and showed how they had identified what caused this issue and pointed out the procedure and the change they implemented to remedy it.
This was a major thing to me, as NCI and Jim Davis had provided me with the tools to find and affect change on products used nationally.
As you implement this culture, the quality of everything you do also improves. Your staff becomes focused on knowing that they and the company are who prevent the preventable.
As bold as this statement seems, we believe we improve our community’s lives by bettering the health and safety of people in northwest Colorado.
By the way, I no longer use a lighter to determine Pass/Fail for combustion safety.
Vic Updike and his wife Amy own Masterworks Mechanical LLC of Craig, CO. Vic has worked in the HVAC Industry as a technician, service manager, as well as other positions for nearly 30 years. If you’d like to learn more about their CO culture, reach out to him at ncilink.com/ContactMe.
Also along with the knowledge of mr Jim Davis if you ever have the chance to attend the heat exchanger experts class its a double whammy, that class was another amazing opportunity.
Jim Davis is the GOAT of carbon monoxide, NCI training, honestly anything that burns fuel of any type… I had the pleasure of installing his new HVAC system, and the knowledge that man holds is mind blowing. ( just don’t get him started on how much the women love his hair lol)
He’s a legend in our industry and an all around great man.