Today, with all the new digital combustion analyzers available, more HVAC contractors are checking equipment efficiency. This efficiency is based on calculations built into the combustion analyzers using an O2 and a flue temperature reading. These are the same calculations once used on the original slide-rule (ncilink.com/SlideRuler) efficiency calculators.
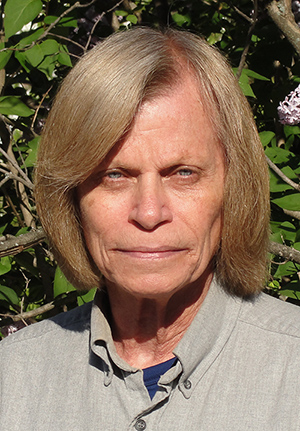
Jim Davis, Senior Instructor, National Comfort Institute
However, unless someone was working on oil equipment, the old slide rule was rarely used. Even when it was, how often did contractors test-in and test-out?
Some Background
In the 1970s and early 1980s, there was an energy crisis and a push to use less fuel. This was the same time the first digital combustion analyzers were introduced.
Testing-in and testing-out became necessary to meet government requirements for tax credits. It is also when people began questioning the ability of these analyzers to calculate actual efficiency.
During that time, servicing and/or upgrading equipment showed little or no efficiency calculation improvement, and in some cases a decline. Yet customers were saving a considerable amount of energy in all situations.
The question in both my mind and the customers’ was Why? Unfortunately, no information on when or how these calculations were developed is available.
Currently, these calculations remain an industry standard and are used to rate the efficiency of all HVAC equipment currently manufactured because that is the way it has always been!
Applying the Laws
Figure 1 lists five sets of combustion readings, on the same piece of natural gas equipment, adjusted with different gas pressures, that all have the same analyzer-calculated efficiency.
Before breaking down the calculations, here are three rules or laws of combustion and energy you need to know:
- The temperature of an object determines the amount of Btus it contains
- Air contains 21% Oxygen and 79% Nitrogen
- Natural gas has an adiabatic flame temperature of 3600o at 0% – O2.
Adiabatic simply means 100% of the energy is available and not lost to any other substance.
In the real world, the substance that absorbs or steals a good percentage of combustion energy is Nitrogen. For every 1% Oxygen in the combustion air, there is 4% Nitrogen. Nitrogen absorbs the heat or cools the flame and makes the energy unavailable for transfer.
Now examine each of the readings, try to avoid being too scientific, and just use some simple math.
Five Examples:
- 12% Oxygen equals 48% Nitrogen.
This cools the flame to 2000o out of a possible 3600o degrees. That equates to 55.5% of the energy being available for transfer.
The flue temperature is 250o; therefore 1750o of heat was transferred.
Divide 1750o by 3600o and you get 48.5% efficiency or transfer. So where did the original 82.2% energy efficiency calculation shown above come from?
- 10% Oxygen equals 40% Nitrogen.
This cools the flame to 2250o out of a possible 3600o. This equals 62.5% of the energy being available for transfer.
The flue temperature is 290o; therefore 1960o of heat was transferred.
Divide 1960o by 3600o and you get 54.4% efficiency or transfer. Again, where did that 82.2% come from?
- 3 8% Oxygen equals 32% Nitrogen.
This cools the flame to 2500o out of a possible 3600o. This equals 69.4% of the energy being available for transfer.
The flue temperature is 3200o; therefore 2180o of heat was transferred.
Divide 2180o by 3600o and you get 60.5% efficiency or transfer. What’s up with this 82.2% in the energy efficiency calculations above?
- 6% Oxygen = 2800o or 77.9% available energy.
The flue temperature is 350o; therefore 2450o of heat was transferred.
Divide 2450o by 3600o and the result is 68.0% efficiency or transfer. Once again I ask where does this 82.2% comes from?
- 4% Oxygen = 3100o or 86.1% available energy.
The flue temperature is 380o, therefore, 2720o of heat was transferred.
Divide 2720o by 3600o equals 75.5% efficiency or transfer. Getting closer!
The calculations in my five scenarios only consider sensible heat and yet there is another loss of latent heat that is not even being considered.
One Last Note
Older combustion analyzers could not calculate efficiency on condensing equipment because of Latent Heat. Today, new calculations have been added for Latent Heat recovery (based on theory) and the calculations are impressive!
15% Oxygen – Flue temperature 90 degrees = 99% efficiency!!!
The point I’m trying to make is that if you depend on the calculated efficiency of a combustion analyzer to determine the actual performance of a piece of equipment, you are being misled.
Maximizing efficiency means adjusting equipment to operate as close to its rated output as possible. Using the formula CFM x DeltaT x ADCF (Air Density Correction Factor) gives you the approximate output.
Keeping oxygen the lowest, flue temperature in a proper range, and carbon monoxide at a safe level will produce the best results. When this is accomplished, efficiency has been maximized.
Hi Jim,
Before I get started, I want to make it very clear that I don’t disagree with your notion that combustion analyzers might not be telling the whole story, and might be giving bad information. That being said, your calculations are based on a terribly incorrect assumption: that the fraction of Nitrogen scales with the fraction of Oxygen.
Atmospheric air, the air all around us, the combustion intake air, and the combustion exhaust air are all about 78% nitrogen. This fraction of nitrogen doesn’t change or scale with different oxygen fractions. The only exception would be small amounts of nitrogen that become NOx at temps greater than 2,200F, but well-tuned HVAC equipment shouldn’t be creating much NOx.
Nitrogen levels shouldn’t be dropping below 75%. Try doing your calculations again, but this time hold nitrogen at 75 to 78% across all of your calculations.
Your article may require finding another culprit to point at, instead of scaling the amount of nitrogen absorbing heat. The percent of heat the nitrogen is absorbing should be the same in each combustion scenario.
Good luck!