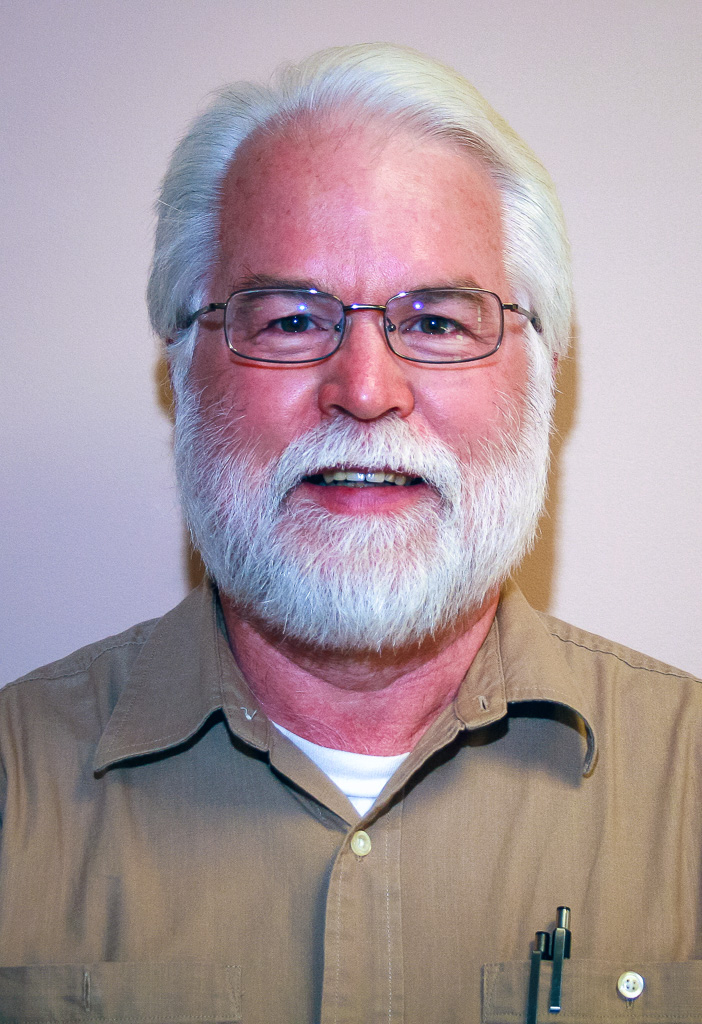
Paul Wieboldt owns Tradewinds Appropriate Technologies, an HVAC contracting firm in Waco, TX.
I am an air conditioning contractor and I have something to confess when it comes to air conditioning equipment sizing: As a community, we don’t measure. We just guess. Probably 95% of us don’t use the right tools for calculating heat loads. We use rules-of-thumb instead.
For example,we have a one-size-fits-all rule: 500 sq. ft. per ton. I call it ‘Manual J 500.’ No complicated math here; divide once, multiply once, and you have your equipment sizing and job pricing done in one shot.
But new energy efficient homes are messing up our game and I don’t mind telling you how.
What happens when a thoroughly entrenched HVAC contractor meets a thermally enhanced building envelope? The answer is the same as when an irresistible force meets an immovable object. It’s usually not pretty. If we don’t change how we design HVAC systems, we might find our trade splat up against a wall someday. That wall will consist of regulators and even third-party engineers taking control and oversight of the residential HVAC industry.
How did Manual J design go from a best practice to a code-enforced regulation? We’ll start with a look back over 40 years of our industry and where our design assumptions have gotten us.
The Good Old Days Sizing Method
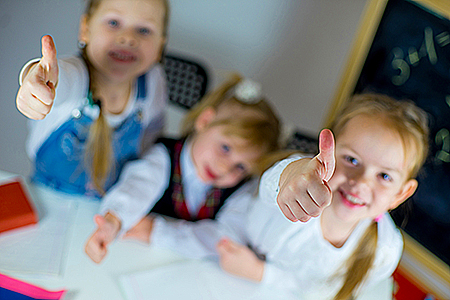
As an industry, we’ve been taught from the outset that sizing HVAC systems is a matter of using the “500” rule of thumb.
For starters, those of us who have been servicing and installing residential air conditioning systems for the last two or three decades pretty much had it figured out that if we sized systems at the ratio of one ton for every five hundred square feet, it generally worked. ‘No difficult load calculations were necessary. Bids were easy to figure. It was as easy as one, two, three. All we needed to do was (1) estimate the square footage of the house, (2) divide that by 500 and (3) multiply by our price per ton and we were done.
For example: Total home size is? 1500 sq. ft. – 500 = ?3 ‘tons.
Next, multiply 3 tons?’ $1200 = $3600.
We did it this way for years and everybody was happy. Well, not everybody.
The Venerable Ventilation Method
In the trades, we are responsible for properly ventilating homes. ‘That’s why they call us Heating, Ventilation and Air Conditioning Contractors. For decades, builders built leaky houses that could breathe on their own. Our biggest ventilation issue concerned arguing with builders about who was responsible for bath fans.
In reality, other trades did the grunt work in terms of providing accidental building ventilation. I am talking about the plumbers and electricians who blasted their right of way for pipes and wires through the building envelope, leaving plenty of room for outside air to move into and out of the house. There wasn’t much need for us to intentionally ventilate a house. If it were up to us the story would end there. They lived happily ever after. THE END.
Let’s Have a War
But the story didn’t end there. The way I heard it, some government bureaucrat asked some university professor how to save energy. The professor had a theory and the government had some money, so they decided to fight a war — the War of Energy Independence. As usual, this was planned as a short, inexpensive skirmish that ‘in theory’ would fix our global energy problems so well and so fast that the oil producing countries would have to find a way to put their excess oil back in the ground. That was in 1974.
For over 40 years now, we have watched the building industry go through numerous energy crises and government fixes. They come like earthquakes and hurricanes; you never know when to expect them, but you know they will come.
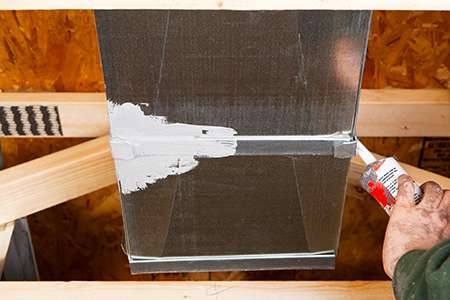
First came the weatherization crews who swept in like mercenaries, caulking and sealing the daylight out of our homes.
The Caulkers Invade During the 1970s and 1980s
First came the weatherization crews of the seventies. They swept in like mercenaries, caulking and sealing the daylight (no joke) out of our homes. They fiercely attacked leaky houses, the enemy of energy independence. But it was like fighting a war with broomsticks and baseball bats. Miles of weather-stripping went up like a Maginot Line. Plumbing and electrical penetration leaks were blasted out of existence with carloads of canned foam. Caulk guns were fired at every crack where the enemy, ‘outside air,’ could infiltrate.
When the battle was over, experts came to assess the battlefield. Shockingly, they found the leaks that were left fought twice as hard as before to let outside air in. The weatherized energy efficient houses of the 1970s and 1980s were just as leaky as before the Caulker Invasion.
The Cold War
The experts mentioned above were some meddling building scientists with research money and nothing better to do. They figured out that HVAC ducts were making houses just as leaky as before! In fact, they found supply ducts leaked so badly outside the conditioned space that they caused the house air pressure to go negative relative to the outdoors. The pressure difference caused small holes to leak more air. Infiltration was just as much a problem as before. The average duct leakage rate was estimated at 30%! Now WE were wasting precious energy resources. It’s not a good feeling to wake up and find that you are the Benedict Arnold in the War of Energy Independence.
Duct Sealing in the 1990s or the
War of Unintended Consequences
Out came the tape and pookey brushes, duct blasters, and legions of duct leakage commandos (Seal Teams?) to the rescue. Ten years of this and then some building science guy figured out there were some serious unintended consequences related to the Duct Sealing Battle.
Basically, they found that ducts were undersized. As an industry, we got away with this for years, because there was always enough leakage for the blower to work under normal pressure. Now fans were acting like they were blowing air through a drinking straw. Poor airflow from undersized SEALED ducts meant that fan motors and compressors became collateral damage.
Typical fans failed when subjected to higher-than-tolerable static pressure. Even powerful ECM motors bit the dust when the amp draw went sky high as ‘silver bullet solution’ fans tried to overcome the new restricted air flow in tight undersized ducts. The resulting lower air flow across the evaporator meant compressors suffered frequent refrigerant flood-back. Bearing wash out and compressor slugging created a slow compressor death spiral. It could take two to three seasons but sure enough one day another compressor becomes a boat anchor.
500 Sq. Ft. Per Ton No Longer Applies
Contractors got along unscathed for 30 years until the foam guys came along and messed everything up. We stuck to our 500 sq. ft. per ton sizing rule, but things didn’t work the same any more. Like Detroit autoworkers, our air conditioners sat idle for long periods with nothing to do.
We put in the same old thermostats that were too dumb to notice rising humidity while the air conditioners sat idle. Even when the air conditioners went to work, they quit early, leaving more humidity hanging around.
Of course, everybody knew enough to blame the insulation contractors for all the problems that arose as a result. Obviously, since we haven’t done anything different for 30 years, how could we be blamed for causing the clammy feeling people were now experiencing. It would be crazy to change the way we do things just because somebody came up with a new insulation.
Now people say the 500 sq. ft. per ton rule no longer works. That’s like telling people Clorox doesn’t kill mold on wood (Another myth. It doesn’t, according to the EPA and many other sources)!
Time to Rant?
So here we are with the big mess made for us by ‘those insulation’ people. Now we must do load calculations for these new super-insulated homes to figure out what we need to do differently with comfort system design.
The average home in the U.S. is maybe 2500 sq. ft. We used to sell five-ton systems to cool that space. Now our calculations tell us we only need half that. So, are we supposed to believe that?
Worse yet, the rated R-value per inch for the typical ‘ pound SPF product is the same as fiberglass batts. So, what gives?
Nothing else in 30 years ever came close to a 1000 sq. ft. per ton. Basically, insulators sold their product and put a big sign on ours, ‘Air Conditioning Systems 50% Off.’ Most HVAC contractors are not ready for this. They are in denial. Too many years of habit and rules of thumb are causing them to react and misinform customers.
To make it worse the Manual J load calculation method is so misunderstood and abused that most contractors don’t trust the results.
?’and Rave
In my HVAC business, we design air conditioning systems for a living. We also test the performance of those systems. We do a lot of them. In fact, in the last few years, since we bought our own spray foam rig (now retired), we have designed air conditioning systems for more houses with spray foam insulation than anything else.
Foam is hard to beat — if properly installed — when it comes to making buildings tight and efficient. I must design mechanical ventilation for every home I foam insulate.
What amazes me is that most contractors I meet don’t install whole house ventilation even though they are VENTILATION contractors. They don’t believe in it. Have you ever met a masonry contractor who didn’t believe in installing concrete? Or a plumber who only provides hot and cold-water supply piping, but no drain waste and VENT piping?
What has Changed?
Here is what I have discovered:
- Manual J is building science. The building shell is a shield from weather. The effectiveness of that shield is what we are measuring
- You can insulate a house so well that it needs as little as half the air conditioning that a comparable house needed 30 or 40 years ago
- HVAC contractors can lower the attic temperature in a cathedralized foam application by more than 50 F, essentially bringing air conditioning ducts back into the same thermal boundary as the occupied conditioned space
- Virtually eliminate the stack effect that robs so much comfort from the typical home.
Here is what we can do:
- Provide comfortable, efficient air conditioning systems in super-insulated homes that will cost half as much to operate and be more comfortable than ever before
- Downsize the air conditioning systems we install in homes that are properly insulated
- Use a blower door to test the building envelope integrity and to establish the correct amount of fresh, cleaned, conditioned outside air to bring into the house
- Consider adding whole house dehumidifiers to maintain comfortable indoor relative humidity in the off-season when air conditioning systems take a prolonged vacation
- Become strategic allies with good insulation contractors so that together we can produce the most efficient, affordable air-conditioned housing available.
Together we might just win this war!
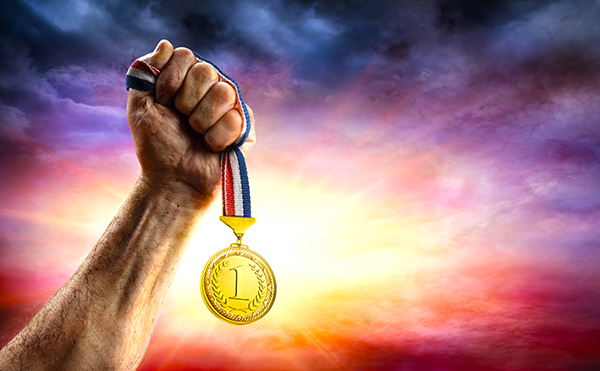
Together, we can win this war. By measuring. Not by guessing. That means no more rules of thumb. Period.
Do the math yourself for an existing home. If the house is well insulated and the windows are low-e high efficiency, then add up the conditioned floor space, divide the conditioned space square footage by the tons of air conditioning installed. If you come up with 500 as an answer, then you have a house designed by the ancient rule of thumb and you need to perform a good Manual J calculation without any fudge factors added.
Don’t have the confidence to do a Manual J you can trust? Find a responsible third-party professional to correctly estimate the tremendous load savings your product brings to the table and use the information to help sell your job.
Paul Wieboldt is a licensed independent HVAC contractor with 25 years’ experience. He teaches HVAC diagnostics and home performance for National Comfort Institute and is a certified testing and balancing supervisor. He is also a NATE-certified technician and proctor. Paul holds certification as a BPI Building Analyst.
His company, Tradewinds Appropriate Technologies, (www.tradewinds-at.com) created Manual J Design Studio (www.manualjdesign.com) to serve the industry by providing nationwide independent third-party load calculations. Tradewinds also conducts Manual J 8 Design software classes. You can email Paul at paul@tradewinds-at.com or call his office at 254 799 1326.
Recent Comments