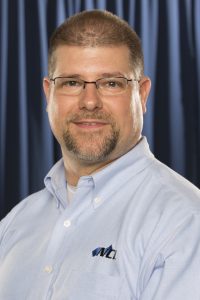
A difficult task that faces many Performance-Based contractors is getting their service team on the same page. If you’ve ever had a technician who seems to consistently leave out that one important piece of information or misdiagnose an obvious system problem, you know what I’m referring to.
How can you assure that your technicians are consistently gathering the right information and correctly diagnosing systems? Let’s look at ways well-built software can help you with the inconsistency challenge and improve your performance-testing results.
Consistent Data Collection
Software lets you predetermine the information your technicians must gather before they can close out a call. They know what’s expected of them on each visit before they step out of their van. Their measurement targets are defined upfront, so everyone aims at the same bullseye.
Controlling the test procedures and readings taken helps reduce callbacks, excuses, and missing information. It helps you hold your guys to a higher level of accountability and removes the temptation to stop measuring performance traits, like static pressure, when you get busy.
Consider this scenario: You dispatch a newer technician to a cooling call where the indoor coil is freezing up. The technician arrives and proceeds to ‘gauge up’ to the system. He scratches his head and decides to add four pounds of refrigerant to the system and call it good.
The next day, the same customer calls back to let you know the indoor coil is still freezing up. You decide to send a more experienced technician out to see what is going on. They have no readings from the day before because the newer technician forgot to write them on the service invoice.
Ouch!
The experienced technician arrives and does a visual inspection of the blower to assure it’s clean and checks the blower speed. Next, they measure static pressure and discover indoor coil pressure drop is high. They pull the coil door off and see the fins are extremely dirty. After a thorough coil cleaning and second pressure drop test to verify improvement, he recovers four pounds of refrigerant from the system because it is now overcharged.
‘Without data, you’re just another person with an opinion.’ – W. Edwards Deming
Consistent data collection and testing procedures in software could have helped prevent this.
The newer technician would have predetermined checks to perform before gauging up and probably would have caught the issue or known to call for help if he couldn’t figure it out.
If a technician with more experience is necessary, he has a clear picture of what to expect since all the newer technician’s information is available for easy access.
Proper Calculations and Improved Diagnostics Using Data

Technicians who test performance will encounter situations that cause readings to look better or worse than they really are. They are often the result of improper calculations and can cause a technician to misdiagnose a system.
Software can help prevent these miscalculations and the errors that come from them.
By predefining the procedures,
Improved diagnostics help technicians match appropriate repairs based on the measurements they input into the software, instead of guessing.
Your technicians can all sing from the same sheet of music since they get their information from a central source. This prevents the unintentional throwing of one tech under the bus by another due to misdiagnosis.
Here’s another scenario to consider: When you dispatch a technician learning to measure total external static pressure (TESP) to a poor cooling complaint. The indoor unit is an upflow gas furnace with an external coil and filter rack on the side.
The tech is excited to measure performance but decides to go off memory. He installs test ports in the supply plenum, after the coil, and in return drop, before the filter.
Unfortunately, this technician chose the wrong locations ‘ the coil and filter should be included in these measurements. This results in readings that are incorrect and much lower than they truly are.
However, he knows from his training that something isn’t right, his TESP is too low.
He decides to call a more experienced technician who helps him discover the error. The experienced tech takes new measurements in the correct locations and identifies the problem as a supply duct restriction that is causing low airflow.
Proper calculations and improved diagnostics available from software would help avoid this issue. The software shows the appropriate fields which reveal correct test locations for necessary measurements. Now the
Correct readings are essential for accurate diagnostics and determining needed repairs.
Service History
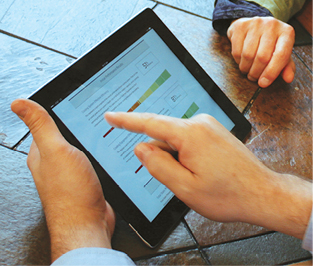
Think about how doctors handle your medical records ‘ all relevant information is in one location that’s quick and easy to search for. In the examples above, service history was an important piece in solving the problem and tracking it.
Your technicians can use service history to review performance measurements from start-up to each maintenance visit. This helps them determine if components are getting dirty, worn down, or unexpected changes occurred.
Many software platforms have document storage that you can tie to a customer or building so the necessary documents are available when needed. Manufacturer’s performance data, fan tables, wiring diagrams, and charging charts are commonly stored documents.
Third Party Data Creates Credibility
Quality improvement guru W. Edwards Deming once said; ‘Without data, you’re just another person with an opinion.’
Unless you have test measurements, you don’t have any data. The reason so many get beat up on price is because they only provide their customers with opinions instead of facts.
Good software enables your customers to make informed decisions from a credible third-party source. You have a partner saying the same thing as you.
Have you ever encountered a customer’s distant relative’s opinion which bears more weight on their decisions than yours? Unless you have data that’s easy to understand, you look like another guy with an opinion.
Software can help your customer understand what is going on with their system and translate your test results in a simple manner. Visual graphics and charts often tell a story to a customer far better than we can express.
Garbage In = Garbage Out
Software isn’t a silver bullet and it can’t take the place of proper training and the skills required to successfully implement it.No software can overcome poorly trained technicians who and don’t have the skill set to successfully test performance.
Software should complement what you’re already doing and make your life easier. If you currently use software, take inventory of your needs and see how it stacks up.
Some companies stick with what they have been using for decades because it’s comfortable, even though it doesn’t fit their current needs.
If you don’t use software, consider the suggestions above as you search for options to use at your company. Above all else, software must be simple to use.
If your techs have a hard time using it, don’t be surprised if they’re unwilling to change.
Recent Comments