When identifying combustion air problems, NCI defines it as a misdirection of combustion air, not the lack of it. NCI also says combustion air affects all burners and equipment in the same room, but that definition goes out the window in the case of sealed combustion.
What is the Explanation for this Condition?
The first time I saw this was also on a two-pipe condensing furnace. The difference was the outside combustion air was piped into the side of the burner box rather than the top and middle. The CO readings were near 1000 ppm!
Adjusting the gas pressure lower diluted the CO readings but did not lower them to an acceptable range. After removing the burner box cover to inspect the burners and the flames, the furnace came back on, and the CO readings were less than 20 ppm and stable.
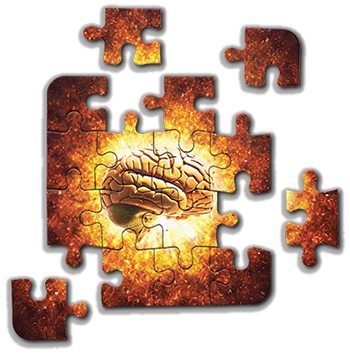
The contractor placed the cover back on the burner box while the furnace was still running, and the CO rose back up. He took it back off, and the CO went back down. What was happening?
I determined that because of the combustion air location in the side of the furnace, most of the air was going to the closest burners. Not enough air was getting to the farthest burner. How does this happen? When the cover is on, you can’t see all the burners. When the cover is off, everything is open to the same amount of air, and there is no problem.
Okay, it was an educated guess. We know how draft hoods can pull flue gases from some heat exchangers, but not all of them. Why couldn’t a draft inducer create a similar problem with air?
Back to the question as to why there wasn’t rising CO? Answer: There was enough draft through the heat exchanger to remove all the flue gases but not enough to bring in enough combustion air to the burners.
Combustion Air or A Mechanical Problem?
Was this a misdirected combustion air issue or a mechanical problem? I would say it could fall into both categories. On the other hand, I would consider this a design flaw and put it in the DAM category.
So it doesn’t matter why this is happening. What matters is what we do about it. After all the service work, the O2% is above 9%, and CO is above 100 ppm. The measurements are close and definitely within industry standards.
Economically is it worth spending more time trying to get this furnace within NCI standards? The answer is no. We must realize that as contractors, our job is to make the equipment do what it can do based on its own rating. Therefore, in this case, we have done our best.
Is it okay for the O2 to be below 6% or for the gas pressure to be lower than 3.5-in.? Any measurement is acceptable if that is what the equipment requires.
One of the first things you learn in the Combustion/CO training is orifices are typically 10% to 15% undersized, which makes gas pressure a token measurement with no real value.
Although most manufactures still list CO2 in their manuals, CO2 can vary up to 10%. We are always making 99.99% of the CO2 if the CO is less than 100 ppm. O2 tells us how much it is diluted and is more accurate.
You are correct in that I should have mentioned if there was any change in the readings with the blower on or off. No change – first thing we watch. Also, if the gas pressure changed with the burner box open, the combustion analyzer would have shown that.
Unlike air conditioning, the blower speed cannot be set correctly until combustion is corrected. Sometimes when airflow is too low you do have to make some adjustments at the same time.
If you are depending on the manufacturer’s blower specs and Delta T, then none of your blowers are set correctly.If you do the math you will see that they don’t make sense.
— Design firing rate does not affect combustion readings.
— Gas pressure verifies nothing.
— Delta T is the same on all furnaces if the blower speed is correct.
Based on the information provided on this article, there is not enough data to properly diagnose the problem; such us:
— Design firing rate vs actual firing rate.
— Design manifold pressure vs actual manifold pressure.
— Design Temperature rise vs actual temperature rise.
Does the manifold pressure change when the burner cover is removed? (Let’s not forget that the gas valve will regulate the manifold pressure based on the burner compartment pressure).
On the combustion side I would like to see the CO, CO2 and O2% levels simultaneously.
Does the combustion data change when the blower turns ON?
It’s like trying to diagnose a refrigeration problem based on refrigerant pressures and Delta-T alone,
In general, it looks like the unit is under firing, hence the high level of oxygen and low stack temperature.
I Believe that beyond economics, we should figure out any problem that we run into, because at times we may lose a day or two but in the long run we gain more knowledge and confidence, and we should charge the equipment owner that time anyway.
Also, the feeling that there’s no problem you cannot solve (within reason) is priceless.
Very informative article Jim. Thank you for the detailed knowledge!