Craftsmanship is a skill in a particular craft that creates something elegant and high-quality. It delivers a lot of value and, within the HVAC industry, a lot of performance. Being craftsmen helps our company, Lakeside Service, build better systems, and to be better in-home service professionals.
The transition didn’t just happen. In fact, it took five to 10 years to get to where we are today, and I don’t know if we will ever truly finish. We first discovered the high-performance approach to HVAC almost two decades ago. At the time, we had no idea where that first airflow class was going to lead us.

Looking back at the road to implementing high performance into our business, we learned many lessons. One that really stuck was we had to build our technicians into craftsmen, not just laborers who punch a clock.
Craftsmanship Begins with Training
Everything starts with training. In 2004, I attended my first NCI airflow class. Shortly after that, we got into performance-based training, but not at a companywide level. I would go to classes with a few of our techs to learn what we didn’t know. We believed this training was the way to go, but we lacked a plan to implement it on a company-wide scale.
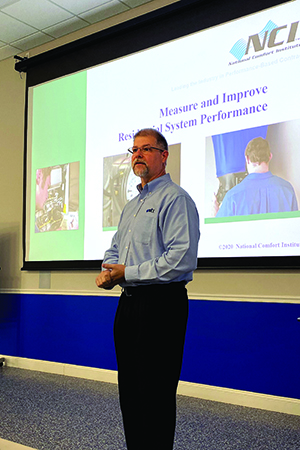
As a company, we always wanted to be the best we could be. So after taking the classes, I realized Lakeside was missing an important design and installation perspective. Airflow is the foundation of diagnostics, not a supplement. There was so much more we could accomplish through testing and measuring static pressures, doing combustion analysis, and even more that wasn’t in our heads yet. I wanted to do it all at once, but that was easier to dream than it was to implement.
So, I became the guinea pig. I’d take the classes and then use what I learned in the field. As I gained experience, we expanded to have a few of our top techs who understood static pressure practice it in the field. I personally gained a lot of experience and skill. However, we just didn’t seem to get the traction to make this our business model.
An unfortunate result is that we created an unintended technician mindset where high performance was for specialists only. Worse, the techs felt it didn’t need to be done every time. Half the guys didn’t understand what we were doing or why we were doing it.
This division became a real leadership challenge when we reached almost 20 techs but only four or five were certified. Imagine coaching a team and only letting the best players learn and practice the plays. How do you think they would perform together on the field? It doesn’t make much sense when I look back on it now, but my hindsight has always been better than my actual vision.
A Different Approach
So, after almost a decade, we changed course in 2012 by doing a National Comfort Institute (NCI) onsite training session for the entire team. Onsite training is where the NCI instructor comes to your business and conducts the exact training they do all across the country. The difference: only your team attends.
Click Below for the Next Page
John, it sounds like your doing most things right; however, you’re missing out on measuring the actual heat loss/gain of the home’s envelope. Without that you will never be doing the best job for the home owner.