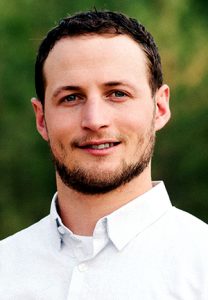
Ben Lipscomb
HVAC equipment manufacturers have a wealth of information about how their equipment should operate under a wide range of conditions. They derive this data from laboratory testing, as well as thermodynamic simulations. However, the lion’s share of it is not made publicly available.
The data they’ publish in product specifications, engineering handbooks, and service manuals is an inadequate subset of all the data. If it was all available, it would be immensely valuable not only to engineers, but also to technicians in the field. If manufacturers have an interest in keeping their equipment operating properly, they should make it easier for the techs to make it so. It’s time to consider today’s more sophisticated technicians when determining the type, format, and accessibility of performance data.
It’s well-documented that to properly maintain, diagnose, and verify HVAC equipment performance is to reference and compare manufacturer instructions and specifications with actual operation. ASHRAE Standard 180[1] lists manufacturer technical material as a source of performance objectives for equipment maintenance. A 2012 evaluation of HVAC maintenance programs[2] in California recommends that utility programs use manufacturer maintenance and diagnostic protocols or compare program methods to them for reference. The advice is also espoused internationally.
It’s time for manufacturers to consider the sophisticated technician when determining the type, format, and accessibility of performance data.
For example, the Australian government repeatedly provides direction to consult manufacturer documentation in its Guide to Best Practice Maintenance & Operation[3], and states that, ‘Easy access to O&M manuals is essential for Maintenance Service Providers to obtain the necessary information.’ The list goes on. However, if you try to put these best-practice recommendations into actual practice, you quickly encounter many hurdles that make it difficult to do so efficiently and correctly.
Manufacturer Reservations
When I’ve spoken with the engineering staff at various manufacturers regarding the data they make public, they tend to have some common rationalizations for providing only limited data. Here are some ways they excuse themselves from the responsibility of publishing more useful performance data:
- ‘The data we publish is only for preliminary design?
- ‘We have additional data available through our system selection software?
- ‘Our data is for use by engineers, not by technicians in the field?
- ‘We only provide our data to authorized dealers?
- ‘We don’t provide data for obsolete products. Check with one of our distributors.’
The truth of the matter is, in the past HVAC technicians often operated on rules of thumb, and most wouldn’t have made use of the data even if manufacturers provided it. We’ve all heard, and maybe some of us have used rules of thumb like these:
- ‘If the suction line feels ‘beer can cold,’ the system charge is correct?
- ‘A 20’F drop across the evaporator means airflow is good?
- ‘A 30’F rise through the condenser means capacity is ok?
- ‘If the flame is blue, it’s burning efficiently.’
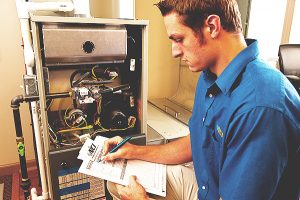
Referencing and recording manufacturer documentation and specifications is the best-practice approach for maintenance, diagnostics, and service.
For systems to operate properly, manufacturer data deficiencies and technician rules of thumb both need to be put in their proper place ‘ behind us! Both groups have a vested interest in coming together to improve field performance evaluation and diagnostics.
Manufacturers want to keep customers comfortable to create brand loyalty. They also want to minimize warranty costs due to improperly installed or adjusted equipment. On the extreme end of their concern spectrum, manufacturers want to minimize liability due to catastrophic equipment failure, carbon-monoxide poisoning, or other high-profile health and safety-related issues arising from a misunderstanding of proper operation.
Just the Facts …
Contractors and technicians also want to build customer loyalty and differentiate themselves from their competition. To do that in a commoditized market like the HVAC industry, contractors must demonstrate value to their customers. One way to do that is to take measurements and compare their results to manufacturer data, showing that the system is operating correctly. Or, if it’s not operating correctly, justifying the recommended course of action (and the price tag that goes with it).
That’s not possible if a tech doesn’t have access to the right data. A high-quality invoice or bid with real data to support it goes a long way toward improving a customer’s perception of a contractor compared to competitors.
Today’s instrumentation — as well as access to the internet through computers, tablets, and smartphones — lay the groundwork for a new generation of sophisticated technicians who can provide a level of service far beyond what was typical in the past. To realize the many benefits of such technicians using manufacturer data appropriately, a broad range of issues need addressing.
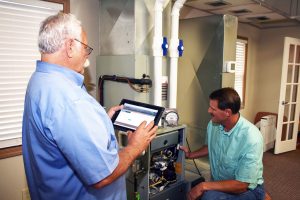
Modern technology should ideally provide field technicians with easy access to the most up to date and relevant equipment data and specifications.
Here are some common barriers for technicians trying to access and use data in the field:
- Access to data is restricted only to authorized distributors or dealers
- Data is unavailable for older equipment, or it’s unclear which equipment generation(s) the data applies to
- Published data is incomplete, or is fragmented, unorganized, and difficult to find
- Data on equipment (e.g. charging charts) are too faded to read, and are unavailable electronically
- Performance data covers a very narrow range of conditions
- Blower performance data applies to specific situation (e.g. ‘wet coil?), with limited or no instruction for interpretation in other scenarios
- Data for individual components, such as coils, is not published for packaged equipment
- Data formats are not standardized, even across different models from the same manufacturer
- Data for field-installed accessories is not provided in equipment specifications, and is not readily available elsewhere
- Data is intended and laid out for use in system design and equipment selection, not field service and diagnostics
- Data is incorrect or inaccurate.
Conclusion
In this article we’ve examined the benefits of referencing manufacturer’s performance data in the field. Using manufacturer data is a commonly cited best practice — manufacturers, contractors, technicians, and customers could all benefit from the industry applying it.
We’ve also listed many of the common barriers that prevent technicians from properly applying manufacturer’s data in their daily work. Issues range from inaccessibility, in-applicability, or even inaccuracy. Today’s technology provides us with the perfect vehicle for delivering the right information in the right format to the right person at the right time. Let’s recognize that one of these ‘right people’ is the technician on the roof, and deliver the necessary data in a format intended specifically for his use.
[1] ANSI/ASHRAE/ACCA 2012, Standard 180-2012, Standard Practice for Inspection and Maintenance of Commercial Building HVAC Systems, Informative Appendix A
[2] California Public Utilities Commission, DNV GL 2014, HVAC Impact Evaluation Final Report WO32 HVAC – Volume 1: Report, Commercial Quality Maintenance Conclusions and Recommendations
[3] Australian Department of Climate Change and Energy Efficiency, 2012, Guide to Best Practice Maintenance & Operation of HVAC Systems for Energy Efficiency
Ben Lipscomb is a Professional Engineer based in Whitefish, Montana. He serves as National Comfort Institute’s Engineering Manager, where he draws on experience in HVAC lab testing, field research, and utility program design to provide technical leadership for the company and consulting services for clients. Ben can be contacted via email at benl@ncihvac.com.
Recent Comments