At Lakeside Service, we have been doing structured and consistent in-house training for the past three years. However, it took us years to create the structure of our program and a lot of effort to keep things as simple as possible.
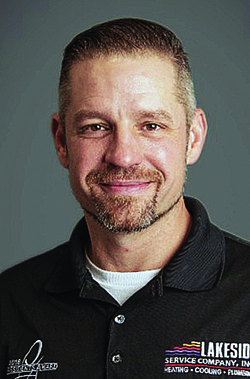
Don’t get me wrong, we have always been strong proponents of training our team – but until three years ago, our training was not organized or necessarily focused on creating career paths to help employees better themselves, earn more money, and have targeted goals to help them do those things.
Why make the career path change? Frankly, it was not only to create a technician corps that was unsurpassed in our marketplace, but it was also a way to help us keep techs happy and loyal to Lakeside Service.
In-house training became the centerpiece of our approach. I have found that doing as much training here and bringing in third party training organizations to help has many more benefits and is ultimately more cost-effective than sending my techs out to external training (though we do some of that as well).
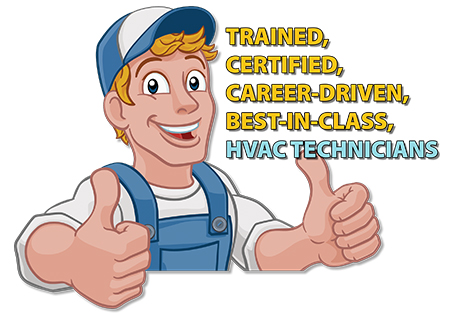
Building a Training Center
Though this is not a requirement, it’s been something I have always wanted to do. We expanded our facility several years ago after a tenant moved out. We used that space to build a working training room with live-fire equipment for hands-on testing.
In 2014, one of my goals was to have all my techs certified in air balancing and CO. Today, I can say that we’ve accomplished that and more.
Training and certification are just some of the ingredients that make the cake. The outcome is using training and certification to build up our techs and create careers at Lakeside.
OUR Overall Training Program Today
Lakeside’s in-house training program typically addresses four areas:
- NATE Certification
- Factory/manufacturer updates and products
- Installation and service best practices
- Specific topics that directly affect our recall percentages.
Our program starts with setting consistent dates and times. For example, we hold classes on installation techniques and practices on Monday mornings. Those classes might include how to correctly pull a vacuum and charge a system, how to commission equipment and set up airflow, brazing, or duct fabrication.
On Thursday mornings, we have service classes. Those include how to diagnose low voltage issues and verify compressor failures or heat exchanger failures. We also cover department issues that are causing recalls. If we notice a trend in recalls, the leadership team discusses what we think are the causes, and design a class to teach processes that reduce unbillable calls.
Click Below for the Next Page:
Recent Comments