When arriving at a job site, you may think you are just out on a service call to get a unit back up and running. The fact is, you are stepping into the newest episode of your favorite investigation television drama. The victim: the refrigerant circuit. The weapon: refrigerant gauges.
Specifically, gauges can be effective for improving performance, or they can be deadly against a compressor. Therefore, most compressors do not die. They are victims of murder.
Direct expansion (DX) HVAC systems use three mass fluid flows to move heat into or out of a building. These include:
- Outside air moving across the condenser coil
- Refrigerant
- Indoor airflow across the evaporator or indoor coil.
To properly charge the refrigerant, all three flows need to work as designed. When technicians overlook the indoor and outdoor airflows and begin adjusting system superheat and subcooling, results can be unpredictable.
First Steps: Setting Up Processes
In California, our utilities require an analysis to verify the results of their incentive programs that focus on maintenance. In one case, testers found little positive impact to adjusting a refrigerant charge unless the system was severely undercharged. Attempting to address the three mass fluid flows by refrigerant charge alone has struggled to show even a 5% average improvement in capacity.
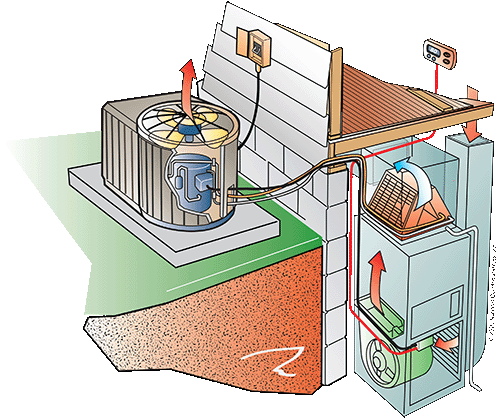
Before attaching gauges to any refrigerant circuit, be sure you have a clear reason for doing so. Setting up a process within your company will ensure uniformity between technicians. Like your favorite CSI television show (ncilink.com/CSItv), you begin by gathering facts.
National Comfort Institute (NCI) shares two points at the start of most of their Performance-Based testing and diagnostics classes: ‘If you don’t measure, you’re just guessing?,’ and ‘without facts, you’re just another person with an opinion.’
What to Look For
So, what do you look for? Some of the evidence NCI discusses in their refrigerant-side performance class include:
- Visual signs a problem may exist
- Proper operating airflows
- Psychometrics and calculations that target suction and liquid line temperatures.
So, before connecting gauges, here is a checklist of items to verify:
- Is airflow within 10% of design?
- Does the static pressure profile meet the pressure budgets?
- Is the indoor coil clean?
- Have you checked that the outdoor coil is clean and unobstructed?
- Is the filter clean and properly sized?
- Are all the registers open?
Click Below for the next page:
Recent Comments