I believe inventory management makes decision-making on many levels a lot easier. It enables us to dispatch the right tech to a job and not worry that they might not have what they need to finish it. Inventory management helps us make purchase decisions. It helps us measure productivity.
Things Don’t Always Go As Planned
We all know that not every job every day goes as planned. In those cases where a tech doesn’t have the right part or tool on their truck, we do have a plan B.
Depending on where the technician is and how soon they need that part, one of our managers will jump in a truck, get it from the distributor, and deliver it to that technician.
Before Kennihan Plumbing and Heating truck inventory management, we used to have several “parts runners” going back and forth from jobs to the distributor.
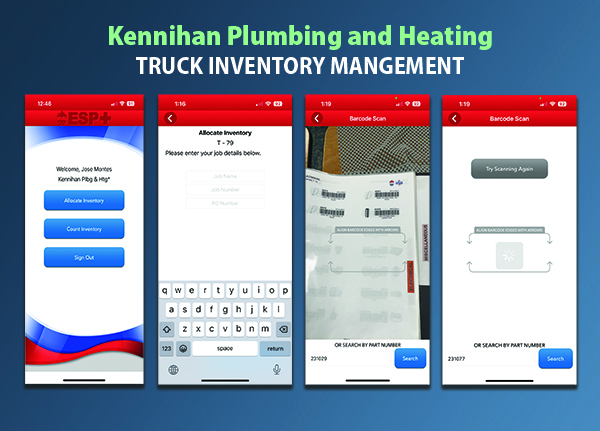
Since we don’t need as many runners now, we took those people and trained them up into maintenance techs or even service techs over time.
What We Learned
By going through this process — again, with the help of R.E. Michel — here is what we learned regarding the steps necessary to get an inventory management system in place:
- Assess Your Needs: This means thoroughly assessing your typical service calls and maintenance tasks to identify the most frequently used parts and tools. You should write it down. Then, decide how many items must be stocked on the truck based on the season. We did this by going back two or three years and looking at what we used the most in the heating and cooling season.
- Create an Inventory Checklist: Based on what we discovered in our assessment, we developed a comprehensive inventory checklist, including essential parts, tools, and consumables per truck. Categorize items based on their frequency of use and criticality for day-to-day operations. Another thing: we took an extra step and asked the techs themselves what they wanted in the truck that we may have missed.
- Establish Replenishment Procedures: This is where R.E. Michel’s ESP program shines. If you aren’t using ESP, you should set up a system for monitoring inventory levels and reordering supplies when stock reaches predetermined levels. You can use inventory management software or manual tracking methods to keep accurate records of usage and replenishment needs.
- Organize Each Service Truck: Optimize the layout of your service truck to maximize space and accessibility. We try to store frequently used items in easily accessible compartments or shelves while storing less frequently used items in secondary storage areas.
- Create a Quality Control Process: This isn’t as difficult as it may sound. It means your tech or service manager regularly checks inventory for damage, expiration dates (if applicable), and overall condition. We learned that it’s important to rotate stock to ensure we use older items first, reducing waste.
- Training and Communication: You should train technicians on best inventory management practices and maintaining a well-stocked service truck. Your distributor may be able to help with this. Encourage open communication between technicians and management regarding inventory needs and any challenges encountered in the field.
High-Performance HVAC Tools and Instruments
Our field service and installation teams measure static pressure and system performance on every call. We follow the standards taught by National Comfort Institute (NCI), and equip them with the tools necessary to succeed. With that in mind, here is what we want on every truck:
Click Below for the Next Page:
Recent Comments