The staff at Austin Energy is comfortable recommending changes in day-to-day installations. They see improvement by following a few rules. These are not actually rules, but a rediscovery of what the HVAC industry practiced in its infancy. While what they discovered is highly encouraging, more work is necessary.
Default Settings
More than half the systems tested in Austin Energy’s system-performance pilot were set up improperly. We found incorrect fan speeds selected on standard blower motors; factory defaults on timed on-and-off fan operation (for harvesting evaporator energy); incorrect fan settings on variable-capacity equipment; and default settings in selectable fields on thermostats for high-end equipment.
Sizing Up Systems
Several studies across our country have proven more than 80% of installed HVAC systems are oversized and deliver only 60% of rated capacity. The good news is that there are methods to identify these issues quickly. The homes Austin Energy surveyed proved this study accurate in their market area. These improvement opportunities should be presented to homeowners. By not informing homeowners, we only perpetuate problems in the HVAC industry.
Total External Static Pressure
HVAC contractors should measure total external static pressure (TESP) as soon as they arrive at a residence. This practice should take precedence over hooking up refrigerant gauges. In almost every home Austin Energy tested during the pilot program, static pressure was a persistent issue.
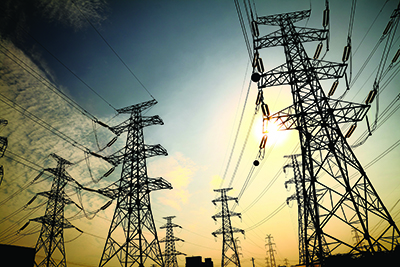
Most importantly, technicians should avoid using the rule of thumb. Industry engineers who design the equipment know what system output is required. Refer to manufacturer specifications and compare them to measured TESP. We can forget static pressure altogether if we shortcut static pressure requirements with rule-of-thumb information.
ΔTs and Interpretation
Temperatures can identify issues early on; however, don’t be fooled. Like superheat and subcooling, without verified airflow present, readings are bogus. A ΔT (Delta T) without validated airflow requirements, can lead us down a meaningless path.
Superheat and subcooling tell us only that the refrigerant charge is matched with the airflow. When the next contractor arrives to fix the issue, they’ll encourage the customer to buy a larger system, thus oversizing occurs. We can be leaving thousands of Btus in equipment capacity unharvested.
Furthermore, many technicians use infrared technology to measure temperature. We should never count on infrared measurements to tune a refrigerant system. Due to emissivity (reflectivity of energy), infrared gives wide variations in temperature readings. It’s better to use an electronic thermometer for all testing and tuning of refrigerant systems.
But don’t throw away the infrared gun. These are very helpful in finding air leakage on the return side of the duct system. Because of the wide diffusion of the infrared beam, small temperature changes show up in a big way.
Return Air
Return air measurements continue to challenge our industry. We continue to follow a trend of increased return air size to provide adequate flow for systems. This includes the practice of increasing the filter area. Seldom will systems of three tons (nominal size) or larger perform with only one high-efficiency air filter. Some systems require commercial grade returns to obtain flows, while others (platform return) may need extensive alteration.
Click Below for the Next Page:
Good information. Thank you,
Joe Moravek