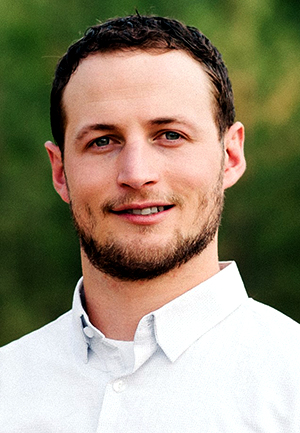
Ben Lipscomb
Last month we looked at commercial performance data from National Comfort Institute (NCI) that showed average commercial HVAC systems deliver just 48% of their specified cooling capacity to the occupied space. Furthermore, you can have two nearly identical commercial systems serving similar spaces that are affected by completely different problems. You won’t know where to start until you test.
It is helpful to know the most common issues, that can lead you towards specific diagnostics. With that in mind, let’s look at the top 10 issues NCI sees on commercial cooling systems.
1) Low Commercial Equipment Airflow
Low equipment airflow is the number one issue contributing to low system performance. Over 60% of HVAC systems have airflow lower than 340 CFM per ton, when the industry standard is 400 CFM per ton
Most equipment will only operate correctly between 350 and 450 CFM per ton.
What’s crazy about this is that technicians often overlook airflow or assume it’s correct and start looking for problems on the refrigerant side of the system.
This oversight leads to misdiagnoses, and often results in mistakes, like adding charge when charge isn’t the problem at all. Low airflow causes low equipment capacity, low superheat, and can lead to coils freezing up or compressor failure. These symptoms translate into higher energy costs and shorter equipment life.
Sometimes low equipment airflow is caused by incorrect fan speed, a fan-belt drive slipping, or pulleys not properly sized or adjusted. If this is the case, the first step is to adjust airflow. As you do this, keep an eye on fan amps and make sure they don’t exceed the maximum rated current for the blower motor. If airflow can’t be increased enough through fan adjustments, it’s time to look deeper into the system.
High static pressure is often the culprit for low fan airflow. High internal static pressures result from dirty or restrictive filters and coils. High external static pressures result from restrictive ducts, closed fire dampers, balancing dampers, restrictive fittings, kinked flex duct, and restrictive grilles and registers.
If restrictions are the issue, profiling static pressure through the system at multiple points can help you identify the most restrictive sections. Then you can make improvements in those sections to help the system breathe.
Common improvement options include increasing duct size or adding ducts, resetting fire dampers, replacing fittings, replacing registers and grilles, straightening and properly supporting flex duct, and re-balancing the system to open up dampers that are throttling airflow more than necessary. After reducing restrictions, re-measure and adjust to achieve the required airflow.
2) High Fan Energy
Some commercial HVAC air handling equipment comes with direct-drive EC (Electronically Commutated) motors, higher horsepower motors, and/or ‘high-static’ drive kits that can help them overcome high static pressures and still achieve appropriate airflows. In these cases, airflow might be adequate, but the fan energy required to deliver that air can represent a major cost.
This is especially true in commercial buildings that must provide continuous ventilation while occupied.
Using the techniques outlined in the low airflow section to identify and reduce airflow restrictions can dramatically reduce fan power requirements, saving energy.
3) Low Enthalpy Change
If airflow across the evaporator is within specifications, but the enthalpy change is lower than about 6.0 Btu per pound for a direct expansion (DX) system (depending on the equipment airflow, outside air, and coil entering temperatures), it’s likely a refrigerant-side issue.
If you suspect this, the first step is to conduct a thorough visual inspection for evidence of leaks, an improperly mounted thermal expansion valve (TXV) bulb, or missing refrigerant line insulation.
After the inspection, it may be time to connect refrigerant gauges for further diagnostics. Whenever you connect gauges you risk refrigerant loss, contamination, or the introduction of non-condensables. Follow all the proper procedures to purge your hoses and minimize the risks.
4) Low Airflow at the Registers or Grilles
If equipment airflow is in spec and you still have low airflow at the registers and grilles, this indicates leakage through the supply or return duct system. Such leaks put air, as well as cooling or heating capacity, where it doesn’t belong: either to the outdoors or into unoccupied and unconditioned spaces.
On the return side, be aware that outside air ventilation and open plenum returns affect how you interpret your measurements.
Taking live system airflow measurements at the equipment, registers, and grilles reveals actual leakage under operating conditions. You’ll find highest leakage through openings closest to the equipment where operating static pressures are highest. These are the most important leaks to address.
Please note: this is not the case when you perform a duct pressurization leakage test, which pressurizes the duct system evenly, potentially making leaks near the registers and grilles seem worse than they are under normal operation.
5) High Temperature Change Through Commercial Supply or Return Duct System
High temperature changes through supply or return ducts indicate thermal losses due to poor duct insulation, poor sealing, or poor space insulation. The temperature difference between the supply air and a poorly insulated space surrounding the ducts can be more than 50’F. This can create a need for duct insulation levels well beyond typical code requirements. One solution is to wrap duct with a four-in. thick (typically R-12 to R-13.5) FSK duct wrap. Another solution is to seal, ventilate, and improve insulation of the space the ducts run through.
Awesome! The 48%? Is that found on (so called) balanced systems or mostly on systems that have never been balanced?
Michael, We’re not really sure actually. All we know is that an NCI-certified technician measured the performance of the existing system and in most cases found deficiencies. I’m sure at least some of them were purported to be balanced.
John,
Thanks for your comment! NCI does offer a multitude of online training options on many of the procedures that would be used to diagnose the issues discussed and score performance. You can check out the catalog of options here: https://www.nationalcomfortinstitute.com/pro/index.cfm?pid=989.
I would also recommend one of our live training options on Commercial System Performance for a very comprehensive certification course that covers a wide variety of testing procedures. You can find information on live training here: https://www.nationalcomfortinstitute.com/pro/index.cfm?pid=940.
Feel free to give us a call at 800-633-7058 if you’d like to talk with somebody about options that might fit your specific needs.
Best regards,
Ben Lipscomb
Good information Mr. Ben Lipscomb.
Are there online tutorials that train testing procedures?
Thank You
John Berg