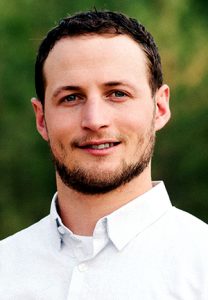
Ben Lipscomb
6) Economizer Failures
NCI data indicates that over 85% of existing economizers are non-functional. While some of this is due to equipment failures, other economizers are intentionally disabled or never hooked up to begin with.
Economizers serve the dual function of providing proper fresh air ventilation and using outside air for cooling when conditions allow. A typical economizer system includes supply and return dampers, a gear drive or linkage and actuator motor to move the dampers, a controller, and multiple temperature or enthalpy sensors.
That is a lot of points of potential failure. Finding the specific problem or problems can range from obvious to extremely difficult.
When faced with an economizer failure, make note of the damper position. If the dampers failed or were screwed shut, fixing the economizer and resetting the minimum ventilation position can actually increase energy use, depending on the climate.
That said, the equipment will now be performing its intended function of supplying outside air while minimizing energy use. If the economizer failed while open, fixing it and setting a lower minimum ventilation position will almost always lead to savings.
If the economizer controls, actuator, or sensors are responsible for the failure, it’s worth considering a retrofit to newer digital controls. Older sensors are notorious for drifting out of calibration.
Digital economizers generally support advanced controls like Demand-Controlled Ventilation (DCV) or variable speed supply fans that can be retrofitted to achieve even higher savings.
7) Uncontrolled Commercial Ventilation
Commercial ventilation is a multi-faceted topic that requires you to consider the outside air supply, as well as the exhaust, return, or make-up air system flows. When ventilation air is supplied through a package unit with an economizer, leakage through closed dampers can often be high enough to meet the design requirements.
It’s important to measure flow rather than assuming it based on damper position. The higher the static pressure, the greater the leakage.
On larger system configurations using separate exhaust systems, a common problem is exhaust not interlocked with outside air supply. In other words, the exhaust system runs on an independent schedule or even 24/7. If you find separate exhaust systems, make sure you understand their function and then ensure they only run when they should.
8) Poor Space Air Distribution
Poor air distribution leads to hot and cold spots within the building. It also contributes to ‘stale’ air in certain areas. It can also cause the system to run longer or shorter than necessary, depending on where the thermostat is in relation to the areas with low or high air currents.
Poor distribution can be caused by many issues including improper placement of grilles and registers, using the wrong type of registers, or a system imbalance.
In the case of poor air distribution, conduct a system performance test that includes register and grille airflows, then compare those to design airflows. If you find the airflows are within tolerance and there are still problems, consider the placement and type of the registers and grilles.
9) Uncomfortable Space Temperature or Humidity
Uncomfortable conditions in the space are often a symptom of one or more of the other issues we’ve covered, but they can also simply be due to occupants in a commercial building messing with the thermostat. Sometimes occupants will engage in ‘thermostat wars,’ where one person is hot and another is cold, and they battle each other by manually adjusting the temperature settings.
This results in the system continually alternating between heating and cooling mode when it could be doing a lot less work if the temperature were locked in at a nice happy medium.
To prevent the war, consider using a physical lockbox around the thermostat or even upgrading to a building automation system that doesn’t provide occupant control access.
Another common issue is that the thermostat cooling setpoint is too low. Setting a low temperature can make a space feel ‘clammy.’ Users often interpret this as being too hot and will attempt to lower the temperature even further.
It’s best to keep the cooling setpoint above 72’F for both comfort and energy conservation purposes. Remember also to inspect to verify the thermostat is sensing the average room air temperature. A large hole behind the thermostat, common in commercial buildings, causes a thermostat to over-cool the zone.
10) Commercial Thermostat Scheduling
Programmable thermostats and building automation systems let you schedule heating, cooling, and ventilation, depending on expected occupancy. However, these schedules are often incorrect because occupants override them, the building schedule changes, no one accounted for daylight savings, holiday settings don’t match the building, or they weren’t set up correctly in the first place. Another issue can be night-time cleaning or maintenance staff turning on the system and forgetting to turn it off.
There are a lot of potential solutions to scheduling issues, ranging from low to high tech. On the low-tech side, night-time cleaning can be scheduled into the system so crews don’t need to touch the thermostat, and thermostat schedules can be reviewed regularly.
On the high-tech side, you can use occupancy sensing control systems to only provide heating, cooling, and ventilation when occupants are present. Additional schedule-related options include:
- Night-time flush to pre-cool the building
- Optimum start and stop to get the building to setpoint by the time occupants get there and ‘drift’ to setback temperatures at the end of the day
- Electric strip heat lockout for optimum start to allow lower-capacity, but higher efficiency heat pump systems to slowly bring space temperatures up on cold mornings before occupants arrive
- Economizer or low stage pre-cooling before the hottest part of the day to slightly overcool the space and defer the need to cool when electric demand and prices are highest.
Problems Are Everywhere – Know How to Find Them
Sometimes when you’re trying to track down issues it can feel like looking for a needle in a haystack. If you’re seeing a system with room for performance improvements and you can’t pinpoint the issue or issues, it might be tempting to think you must be doing something wrong and simply walk away.
Don’t! Perfect commercial systems are about as rare as unicorns ‘ they just don’t exist. NCI data shows that virtually 100% of existing systems have at least one problem when they are tested in, and over 90% of them have multiple problems.
Isn’t it helpful to know there’s room for improvement on almost every system out there? It’s nice to feel needed and know there is opportunity to improve every system.
Ben Lipscomb is a registered Professional Engineer with more than 14 years’ experience in the HVAC industry. This experience includes laboratory and field research, Design/Build contracting, and utility energy efficiency program design. He is National Comfort Institute’s engineering manager and may be contacted at benl@ncihvac.com.
Awesome! The 48%? Is that found on (so called) balanced systems or mostly on systems that have never been balanced?
Michael, We’re not really sure actually. All we know is that an NCI-certified technician measured the performance of the existing system and in most cases found deficiencies. I’m sure at least some of them were purported to be balanced.
John,
Thanks for your comment! NCI does offer a multitude of online training options on many of the procedures that would be used to diagnose the issues discussed and score performance. You can check out the catalog of options here: https://www.nationalcomfortinstitute.com/pro/index.cfm?pid=989.
I would also recommend one of our live training options on Commercial System Performance for a very comprehensive certification course that covers a wide variety of testing procedures. You can find information on live training here: https://www.nationalcomfortinstitute.com/pro/index.cfm?pid=940.
Feel free to give us a call at 800-633-7058 if you’d like to talk with somebody about options that might fit your specific needs.
Best regards,
Ben Lipscomb
Good information Mr. Ben Lipscomb.
Are there online tutorials that train testing procedures?
Thank You
John Berg