Equipment Temperature Measurements
Your physician compares your temperature reading to a known standard to see where it compares. A healthy person should be at 98.6’F. If the measured temperature is out of range, it’s an indicator that something could be wrong and further investigation is necessary.
Just as a medical professional has an acceptable test location and baseline to compare their readings, so should we as we follow a similar pattern with temperature testing. We need to test in the right locations and then compare our measurements to known standards to see where we fall. Only then should we decide if we need to take further actions.
The first step with equipment temperature testing is to assure your test locations are acceptable. A simple rule to follow is to place your test ports where the thermometer probe cannot ‘see’ the heat exchanger or evaporator coil. It’s also a good idea to avoid testing near any duct leaks or the blower motor. NCI recommends you test equipment supply temperatures in a branch duct close to the plenum.
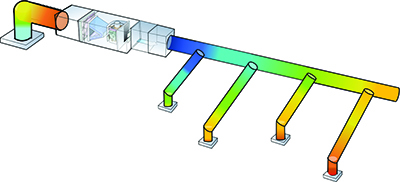
As you measure and interpret equipment temperature changes, keep in mind it is always affected by the volume of airflow moving through the equipment.
If airflow is lower than specified, the temperature change will be high. If airflow is high, the temperature change will be low. Remember, ‘A’ is before ‘T’ in PATH. This is another reason why you should always check airflow first.
When you measure equipment temperatures, begin with the dry bulb difference or Delta T (‘t) between the air entering and exiting the equipment. Compare your readings to the specified ‘t for the equipment you’re working on. Gas furnace ‘t is the easiest to find. The nameplate inside the furnace provides the temperature rise range.
Air source equipment, like heat pumps and straight cooling systems, have a varying ‘t based on various conditions. Heat pump heating ‘t ranges are usually between 10′ to 35’ depending on the outdoor air temperature. The warmer it is outside, the higher the ‘t.
Cooling system ‘t ranges are typically between 16’ to 24?. Factors affecting this range are airflow across the coil, indoor dry bulb , indoor humidity, and outdoor air temperature.
If your airflow is within – 10% of manufacturer specifications and the equipment ‘t is within range, chances are high the equipment is operating as designed.
However, just because the equipment airflow and temperatures are in range, it doesn’t mean the system will maintain comfortable conditions. This is where system temperatures can help you see through a fresh set of lenses to identify hidden defects.
System Temperature Measurements
When your temperature measurement locations move beyond the equipment to the registers and grilles, you start to understand how duct system insulation influences performance. This test allows you to see the ‘t your customer experiences in their home or office. Unfortunately, it is usually nowhere near the same as the equipment ‘t.
In an ideal world, the equipment ‘t and system ‘t would be the same. However, we put duct systems in some rough locations. They are subject to extreme temperatures that change the conditioned air temperatures through them.
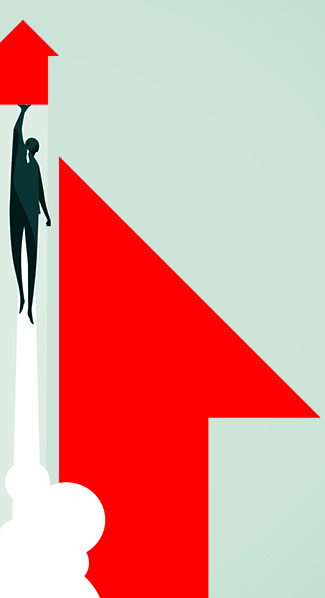
To account for these conditions, you can measure system temperatures at these common test locations:
- The temperature in the farthest supply register and return grille to determine worst-case system ‘t
- The average of three supply register temperatures and two return grille temperatures to determine average system ‘t (We’ll discuss this concept more in the next article)
- At the supply register and return grille of the most uncomfortable room.
For your system temperature readings to make sense, you’ll need a standard to compare them against. You could aim to duplicate the equipment ‘t, but you will find yourself disappointed that you rarely hit that target. A more reasonable goal for a well-insulated duct system should be less than 10% loss of the equipment’s ‘t. That might sound like a lot until you see how hard it is to come in under that target. Here’s how you can figure it out for yourself.
Click below to go to the next page
Recent Comments