If we are working on a system with a gas furnace, we can figure this out with a bit of math. I look at the system’s data plate and find the temperature rise range. Whatever the range is, you want to find the midpoint of the temperature rise.
Find the Midpoint Temperature
The midpoint temperature will be the target. Running a furnace at the midpoint of the temperature range will give you a buffer against issues like when the furnace filter loads up with dirt.
You find the temperature midpoint by simply averaging the larger and smaller numbers.
So let’s say your range is 20°F to 50°F. Take the larger number and add the smaller number together, then divide by 2.
In this case: 50°F + 20°F = 70°÷2 = 35°F.
That 35°F is your target heating temperature rise.
Finally, we can solve for our target airflow by slightly rearranging the sensible heat formula:
BTU Output ÷ (temp rise x 1.08) = Required heating airflow
Now that I have my required airflow for the customer’s system, I start looking at the ductwork near equipment components.
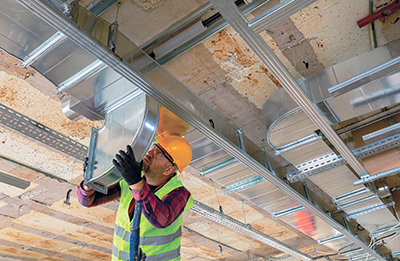
Two numbers that I want you to remember are 700 feet per minute (FPM) and 900 FPM. These numbers are the maximum velocity limits that ACCA recommends on a residential duct system. The first number, 700 FPM, is for the return, and 900 FPM is for the supply.
We can analyze the return and supply trunks with these numbers in mind. If you have a Ductulator, then it is easy. Plug in the duct size you are referencing and look at the CFM you are moving and the corresponding velocity. If it is above the maximum
velocity limits, the system is oversized, the ductwork is undersized, or, worst case, all of the above.
Sizing and Other Potential Issues
Remember that just because the velocity in the duct is less than ACCA’s limits does not necessarily mean the duct is sized correctly. It means no glaring red flag is waving in front of your face.
Another obvious issue might be a small evaporator coil on a large system. This would cause a high-pressure drop across the evaporator coil.
I always look at the filter size as well. The magic velocity I use for 1-in. filters is 300 FPM. If your velocity is higher than 300 FPM, it is likely causing a high-pressure drop, increasing the static pressure.
Converting filter CFM to velocity: CFM ÷ Area (sq. ft.) = velocity
Let’s say our hypothetical system moves 1,000 CFM through a 16-in. x 20-in. filter.

In this example, you can see that a 16-in. x 20-in. filter is inadequate for the system.
Taking National Comfort Institute’s “Duct System Optimization” class was also crucial to my process. It taught me how to identify duct system deficiencies and make surgical changes to the ductwork that positively impact the overall system performance.
Click Below to Go to the Next Page:
Is this article available as a PDF?
How is it possible to do an accurate manual J on a house that is not new ?
Hey Scott, here is a link for the PDF of the issue: https://hvactoday.com/monthly-issue.
I think you are absolutely right; performing an accurate Manual J can be tricky on existing homes. I start off by referencing building codes that were active at the time the home was built. I also look at the windows and doors to see if they look like they have been replaced. If they have been, and the U-values and other data is unknown, then I use the generic tables in Man J.
There are also tricks to figure out how many panes of glass and so on. You can get really fancy and use a website called recalc.com.” They have a calculator where you can take the Delta T of a surface temperature and it will estimate the R value for you. Overall I would say performing a load calculation on an existing home is more of an art than a science. If the values are unknown, do your best to guestimate. So far I have not had any jobs that have come back to haunt me.