A Safety Culture Requires Continuous Improvement
This process is a focus on continuous improvement. Between our approach of no-blame and engaging the right stakeholders, we create a community that focuses on the big safety issues and on daily suggestions to help avoid minor issues. Such suggestions include getting better work gloves, PPE, or safety glasses.
Then it is up to the leadership to go to their resources and have samples brought in for the team to examine. The team then decides what works best for them. They own the decision. And I think when you create that type of engagement, it creates people who are champions. That is our culture.
So safety is not just a leader’s responsibility. It is also the team’s responsibility.
The Safety Committee is a peer-to-peer program developed and fostered by Dwayne Stauffer. Furthermore, this process also works to help improve minor injuries such as sprains and strains. We also regularly talk about these injuries and encourage team members to stretch before beginning work to help prevent them.
Company Size Does Not Matter
Even though Haller is such a large company, this kind of safety culture is transferrable to companies of any size. Smaller companies may not have dedicated safety leadership on staff, but they should have someone with safety as one of their responsibilities. The key is to create a peer-to-peer culture of inclusion and a no-blame approach to safety events.
There are two key things a smaller company should think about: First, as an owner or general manager, you must break the habit of having all the answers. Your role is to facilitate. Let everyone speak freely.
Secondly, when you include others, safety becomes part of their responsibilities. In a small company, that would be incredibly powerful.
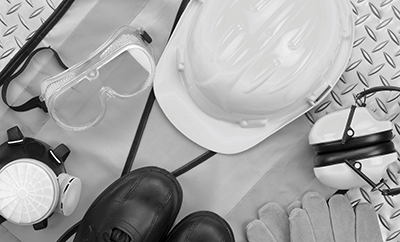
Training is as Important to Safety as it is To Skills
For you to create and foster a culture of safety, you need regular and continuous training. There are many sources for this training from national sources through the Occupational Health and Safety Administration (OSHA) and third-party outfits like NCI.
When it comes to HVAC services and construction, we focus on Combustion Performance & CO Safety (ncilink.com/COTest)
training provided by NCI. We usually bring their trainers in to train all our field guys over several days.
We also focus on OSHA training. Specifically, we do OSHA 10-hour training (ncilink.com/OSHA10) for all our employees. This online training program covers fall protection, personal protective equipment (PPE), electrocution protection, ISHA inspection procedures, and more.
For our foremen, we recently began using the OSHA 30-hour training (ncilink.com/OSHA30). Furthermore, we do what is known as confined space training (forklift training) and more.
Don’t Forget Internal Safety Training
Internal Training: For a company of our size, we use an outside training consultant to organize programs customized for our needs. This consultant also provides advice and guidance. When he puts on a training program, it’s all hands-on, and in many cases, training is on-site.
By the way, we design our training approach to be engaging and interactive. We’ve found if you don’t use this approach, it usually doesn’t work. No matter what size your company is, you need to find a way to engage your technicians so they can relate to it. Engagement makes training real for techs.
Part of that is making sure the techs understand the “why” behind safety. Remember, techs are diagnosticians. They are good at tracing problems to the root cause, doing root cause analysis, and finding solutions. The same should be valid for your approach to safety and your training.
Click Below for the Next Page:
Recent Comments