Full Flow Pump Test
After confirming the “no-flow” DP reading, we test the pump flow with all control valves open. Do this by taking an operating DP reading of the pump. We then plot that DP reading (in head of feet) on the pump curve to determine full flow (GPM).
If the measured flow rate of the pump is below the required connected load, then you need to calculate what percentage of the pump flow equates to the connected load. Then we balance the hydronic loads to the individual specified flow rate percentage.
For example, if a pump tests out providing 85% of the full connected load, re-calculate each design flow at 85%. The theory is that the building heating system may never operate in a condition where all heating valves are calling for 100% flow. When operating during a typical heating day, there should be enough pump capacity to achieve the individual flow rate for the hydronic loads.
On the other hand, if the pump flow rate is at 120% of the required full load, then reduce the pump capacity by approximately 15% before balancing the hydronic loads.
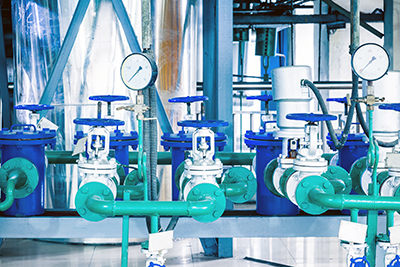
Additional Tips
We do not decrease the pump capacity further because we add more DP to the system as the loads are balanced. We must leave some added capacity when balancing the loads as the operating DP will increase, and the pump flow rate will decrease. Adding capacity can be done by adjusting the discharge valve on the pump and taking another DP reading to verify the revised flow rate on the pump curve.
Another possibility is to install a manual balance valve at the pump discharge to measure and readjust the flow rate if the pump is operated with a VFD (variable frequency drive). The TAB technician must then use the pump affinity laws to determine the new operating speed of the pump/motor.
The VFD can be adjusted lower to achieve the desired beginning flow rate. Conduct another “no-flow” DP test on the pump and re-plot your curve with the slower operating speed. A new operating DP reading will allow you to verify the revised pump flow with the revised re-plotted pump curve at a lower speed.
Hydronic Load Test and Balancing
The next step is to start the actual water balancing of the loads. I first review the system and look for what I call “water hogs.” Water hogs are loads with larger flow rates and can be found with secondary pumps, unit heaters, and cabinet unit heaters.
At Integrity, we will balance the larger hydronic loads with secondary pumps by first de-coupling the pump from the primary heating mains. We do this by toggling the heating valve to no call for heat.
The pump recirculates water through the coil and will be isolated from the heating mains (de-coupled).
Then we do a preliminary pump test by taking DP/Flow readings with the pump circulating fluid through the coil and then a no-flow test to verify the impeller size.
If the system has manual balance valves, use them to balance the final pump flow.
After balancing the secondary pump circuit when de-coupled from the system, toggle the control valve to the fully open position. We can now adjust the balance valve on the load return line connected to the return main to achieve the specified flow rate of the load.
We then proceed to water balance the remaining water hogs.
After the first pass on the hydronic system, we go back to the primary pump and start water balancing the entire system in numerical sequence. As we proceed through the system, we recheck previously balanced loads and make further adjustments as needed.
For any loads that were low on the first pass of testing, you can go back and make another complete pass on the system. Or you can retest any loads that were low on the initial pass. The flow should increase at those loads as the system is balanced.
Click Below for the Next Page:
Recent Comments