A common misconception in our industry is Carbon Monoxide (CO), is a heating season issue. When we look at the evidence, nothing could be further from the truth.
Many CO incidents in homes originate from water heaters not venting properly. While the appliance may not be the actual cause, it’s typically the first that will stop venting, dropping Carbon Dioxide (CO2), into the burners. This causes incomplete combustion which generates CO.
So what causes water heaters to improperly vent flue gases? Typically it’s the pressure in the space where the appliance is located becoming more negative than the draft in the flue.
Instead of drawing gases out, the flue works backwards, pulling in outside air. This air can block the flue gas causing CO2 to fill the burner area resulting in incomplete combustion.
Why It Can Be Worse IN WARM Weather
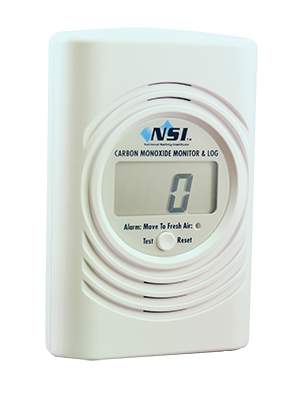
monoxide monitor family.
Most pressure imbalances in homes are caused by leaky ductwork and/or poorly balanced HVAC systems. In some cases building envelope issues can increase these imbalances.
When a forced air system switches from heating to cooling, the blower usually kicks up to a higher speed to move more Cubic Feet per Minute (CFM) of air through the ductwork and into the home.
When this happens any pressure imbalances will increase significantly, making the likelihood of poor venting greater than in winter.
This is just one of many reasons technicians should check for CO during service and maintenance visits. Other CO sources include improperly venting pool heaters, fireplaces, BBQ grills, stoves, generators, and so forth.
But you can’t always be there to safeguard your customers’ homes, so the next best thing is a high-quality low-level CO monitor.
A Quality LOW-Level CO Monitor
There are three important things to look for in a high-quality low-level CO monitor:
- It should alert the occupants when there is a level high enough to affect their health – especially infants, children, and the elderly.
- It uses a high-quality, reliable electro-chemical sensor similar to what is used in professional CO/Combustion analyzers.
- It’s only sold by professionals who educate homeowners and know how to respond when the monitor signals dangerous CO levels.
A high-quality monitor should have different alert levels and sounds. The first alarm sounds typically at 15 PPM (Parts Per Million), and then a stronger alert at 35 PPM. The monitor should go into full alarm mode at 70 PPM with no delay.
Unfortunately, typical store-bought detectors have none of these features, and most are never tested at the factory. Because of UL Standards, these detectors do not go into full alarm unless levels exceed 70 PPM for up to 4 hours!
A healthy adult could easily not wake up after an hour or less at 70 PPM. A child or elderly person would succumb in even less time.
Everyone deserves to know the difference between store-bought detectors and professional grade monitors. It could save their lives!
For more than two decades NCI has been providing National Safety Institute (NSI) Low-level Monitors. Our second generation NSI 6000 meets all of the criteria outlined above.
The monitor also has Bluetooth features that allow data from the monitor to be stored in the cloud for easy access and analysis. Visit nationalsafetyinstruments.com to learn more.
The bottom line is CO never takes a day off. It can strike at any time. However, with the right training and tools, you can minimize the chances of your customer becoming its next victim.
Recent Comments