Rubber, Meet Road
Over the course of four days, we completely revolutionized the heating system. Aside from the baseboard and some copper pipe, we replaced everything. As is usually the case when you think things through before grabbing a pipe cutter, the install was relatively straightforward.
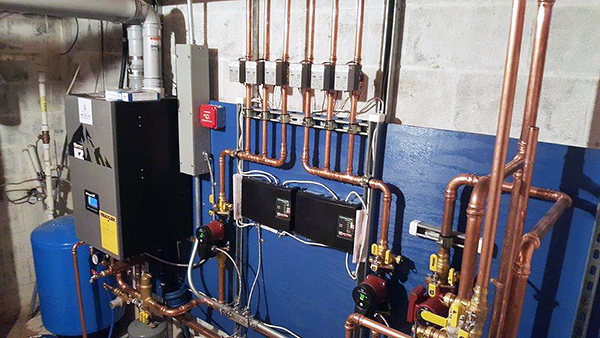
My apprentice, Ben Dyson, and I installed a K2 condensing boiler made by U.S. Boiler Company. Considering the efficiency increase from 80% to 95% AFUE, and the fact that we actually sized it properly, we expected at least a 30% reduction in energy spend.
We divided the existing supply and return piping into six zones, separating the upstairs and downstairs and creating a few new zones in the process.
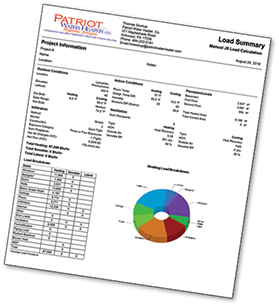
In addition, we added a
Fine-Tuned Success
I visited the home on the morning after I fired the boiler, and the customer mentioned how nice it was to have even heat throughout the house. At the time, the outdoor temperature was 31’F and the boiler was running at 20% input. Nonetheless, there was still a little room for improvement.’
Through the K2 boiler’s touchscreen display, we accessed the zone-by-zone runtime data and noticed that the living room was calling for heat too often. So, we lowered the anticipated Btus slightly on the boiler’s Sage Zone Control and set the programmable thermostat’s temperature differential from one to two degrees. That solved the issue.
That’s what I love about these. Once I program the control, I can get really granular by looking at individual parts of the system. This allows me to fine-tune the system. If you plan to install a modulating boiler, isn’t fine-tuning the ultimate goal?
On commercial projects specifically, we’ve begun installing a meter on the gas valves of the systems we will be retrofitting, sometimes a year in advance. It’s a fantastic way to compare the energy use before and after a retrofit, and we can use those concrete numbers to sell the next project.
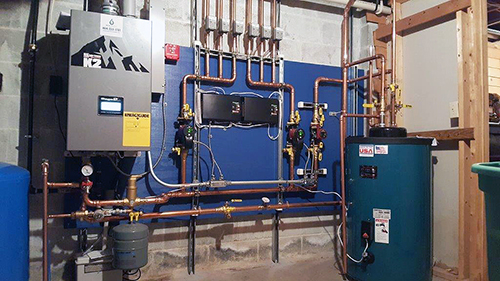
For residential jobs like this ‘ which don’t typically provide us with enough data collection time on the front end ‘ we use the owner’s records.
On this job, the owners knew they’d used 2,200 gallons of fuel oil (308,000 MBH) the previous year. The year following the retrofit required 800 gallons of LP gas (73,600 MBH). Those numbers don’t include DHW production either. Why? Because we removed the electric DHW supply and now
That’s a staggering improvement, but at the end of a cold winter day, it is pretty hard to quantify comfort.
Tom Soukup is the principal of Patriot Water Heater Co. with over 20 years as a hydronic designer and installer. He specializes in high-efficiency and green technology and brings his expertise to custom commercial work, pool heating, and agricultural projects. You can reach him at twsoukup@patriotwaterheater.com.
Recent Comments