Furthermore, Arzel is using this time to dedicating a separate room within their building focused only on webinars.
Barton adds that the next phase is bringing their content into podcasts, live streams, as well as online live guest speakers who can be interviewed and who can interact with their contractor customers.
Other Training Options
Also, any contractor or distributor can sign up for their own personalized, one-on-one Arzel webinar on the date and time of their choice. Barton explains that this enables them, for example, to provide targeted training to a salesperson who wants a better understanding of the product and how to sell or design it. He or she can set up a course at their convenience and even from home.
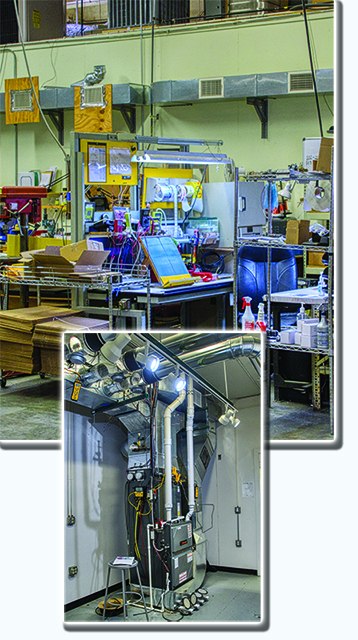
Below: Comfort College, since its inception, has offered contractors training on the use, design, and troubleshooting of Arzel Zoning systems. Here they can test airflow, static pressure, and see the impact of dampers on a live furnace.
‘We can also focus on a company where the contractor can have their entire crew take a deep technical dive into zoning and airflow.
‘There’s no reason we can’t facilitate that from our facility and broadcast to their facility. Live online training is interactive, and the technicians can ask questions and get answers.
‘It’s all about putting ourselves out there and making sure that we are available when needed.’
The National Comfort Institute Connection
Historically, through their Contractor College, National Comfort Institute (NCI) and Arzel collaborated to understand better the dynamics of airflow on the entire HVAC system. This includes the impact of static pressure. According to Barton, it is also where the two organizations took a deep dive into what happens inside a bypass on a zoned system.
‘With NCI’s knowledge and their help working with us in our lab, we developed the bypass sizing chart that we still use today,’ he says.
‘We explored the actual velocities and CFMs going through a bypass and often found they were off the charts from what we thought they would be. It was NCI that opened our eyes to all of this.
Another connecting point is what Barton calls NCI’s laser focus on high-performance contractors and their teams. He says, ‘We love this group of customers because they strive to be the absolute best they can be. We’ve seen this first-hand at NCI events like Summit, where contractors share knowledge and network together to help each other understand and use performance to better their customers and their companies.
Barton continues, ‘It’s obvious they don’t want to be a typical heating and air conditioning company. They want to differentiate themselves and to be educated on doing things the right way. They are the exact people we want to partner and work with.’
Arzel Today and Tomorrow
The Arzel Zoning Technologies workforce is divided into several working groups that include their technical/engineering department (product development), the manufacturing team (production and assembly), and their sales/marketing group.
All production and assembly, warehousing, and shipping are done in-house. They bring their products to market through a close-knit wholesale distribution network but work very hard to maintain strong bonds with their contractor customers through training.
Today there are several other zoning product manufacturers on the market. According to Barton, Arzel stands out in how accessible they make themselves to contractor customers.
Click Below for the next page
Recent Comments