‘I knew someone who was working at Arzel at the time, and I called him to see if he could help me find some folks. He told me that Arzel was in the same boat ‘ looking for someone to join their tech team. It sounded ideal for me, especially since I was so passionate about their product and had been using it for so long. I asked if I could apply. The next thing I know, I was hired!?
That was 13 years ago.
Today the company is preparing itself for what Barton says is a potential resurgence of demand after the COVID pandemic comes under control and orders begin to climb to pre-pandemic levels and beyond.
He says that Arzel, like every other business in America, felt the impact of people becoming ill and being forced to social distance. Though the company remained strong in 2020, it did see shipments fall off, and some team members became sick with the virus.
Barton adds that the secret to keeping things going was taking the time to prepare for the resurgence of business by upping their game in terms of education ‘ the cornerstone of Arzel’s relationship building with contractors since its founding.
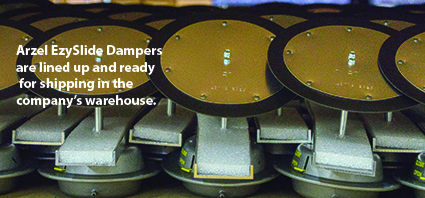
It Is All About Training
He says, ‘Arzel has always provided training and support for its products and services ‘ from system design to troubleshooting. We have always put a strong emphasis on contractor training. We’re proud of our training facility. It’s home of our on-going Comfort College (ncilink.com/ComfortCollege) program.’
Since its inauguration, Arzel’s Comfort College has offered hands-on lab training sessions where HVAC contractors receive product training, zoning install techniques, and design concepts. Arzel has a strong commitment to the industry through its alliance with NATE to provide attendees with accreditation towards NATE recertification in all installation and service areas (except refrigeration).
Like everywhere else, things had to change in terms of in-person training, and Arzel’s Comfort College was no different. Remote learning became so much more important.
Plus, according to Barton, some pre-COVID expansion and renovation of the in-person classroom area now allow for students’ social distancing in a comfortable and socially-distanced environment.
‘We are also in the process of updating our lab area where students get to see first-hand operational HVAC equipment paired with Arzel zoning controls. This part of our training and educational programming allows students to get hands-on with installations where they can physically get in there and install dampers, run tubing, and so on.
Hands on Arzel Zoning Training is Vital
‘Also, we conduct airflow dynamics training in those labs,’ Barton says. ‘This is where students use airflow hoods and pressure instruments to take readings. It all comes together with our bypass and Airflow Dynamics training. It’s during this segment of our program where we often see contractors have that ‘Ah ha!’ moment where they suddenly can see how it all makes sense.
‘In other words, they not only come to understand why zoning can be so beneficial, but they also see how it provides them a great tool to resolve customer comfort issues.’
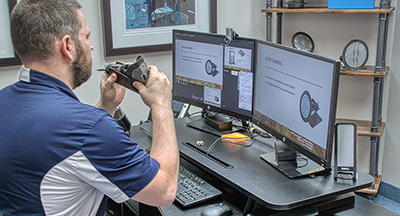
Barton emphasizes that training has always been a critical part of the Arzel approach to business. ‘We have always tried to improve and reinvent ourselves,’ he explains, ‘and that’s never been more evident than in 2020 with the pandemic.’
From the aspect of conducting online and webinar-based training, this isn’t anything new to Arzel. Barton says the company has used such tools for training for years.
‘However, once the pandemic swept the nation, we needed to up our game and find even more ways to get our contractors what they need and what they want. That process is still underway now. We began developing new and more diversified content. We also put together a pre-recorded library of webinars and have them available on our website through our contractor portal.’
Click below for the next page:
Recent Comments