When you find yourself in a position where you can’t seem to achieve an air or water flow specification, that, in my opinion, is when the fun begins. You must ask yourself, “Why.”
Our company excels at analytical testing to discover the reason why. Going the extra mile to find the reason for poor performance has greatly enhanced our reputation in the industry.
We follow this process at Integrity Test & Balance, Inc. As TAB (Testing, Adjusting, and Balancing) contractors, we come in after the mechanical contractor has completed his work and test the system to ensure it operates as designed.
Feel free to use this in your business to help determine why commercial system performance isn’t what it should be.
Checking the Specification Requirements
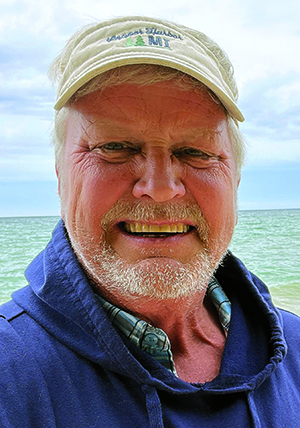
After securing a project, we examine the specification requirements and compare them to our hydronic test and balance plans. We do this to ensure we can achieve the flow specifications.
The first step is to compose the required testing and balancing reports with the design documents. We gather all the design documents, including the project specification booklet, addendums, and any bulletins to date, along with a complete set of reviewed and approved equipment submittals.
The key here is to verify that the equipment submittals have the “Reviewed and Approved” stamp on it. This is very important. If you use equipment submittals that don’t have the “Approved” stamp, you risk the possibility that the equipment was rejected, and the supplier had to “Re-Submit” per the engineer’s correction notes. That means there may be changes to the equipment that you need to know about.
I can’t emphasize enough the need for an up-to-date set of mechanical plans. I’ve known of some construction management companies who will confiscate outdated project prints. If this happens, it will set you back because you must acquire the latest prints approved “FOR CONSTRUCTION.” Don’t ever let that happen.
Pump Test Reports
We start by composing Pump Test Reports by viewing both the hydronic equipment schedule pages and the approved pump and hydronic submittals. In that report we list all the required design information on the pumps, including flow rate (GPM), operating head differential (DP), voltage, rated horsepower (HP), and brake horsepower (BHP). We also include design pump speed (RPM) and operating frequency (HZ) if the pump is controlled by a variable frequency drive (VFD).
We review both the hydronic equipment schedule and approved submittals to see if there are any significant discrepancies between the two. The design operating DP and the submitted operating DP should be the same. The design engineer calculates the DP, and the pump suppliers should base their pump selection on the same, along with the pump model number.
Hydronic Load Test Report
Next, we review our TAB estimate and the mechanical schedule pages to determine the count for hydronic equipment and loads. We also check each hydronic load and the specified flow rate (GPM).
Click Below for the Next Page:
Recent Comments