It’s more important than ever to measure and tune performance on HVAC systems with high-efficiency equipment. Getting equipment to achieve its design capacity is highly dependent on two key variables:
- Airflow across the heat exchanger (in fossil fuel furnaces) or across the indoor coil (in Direct Expansion (DX) air conditioners and heat pumps).
- Proper fuel/oxygen ratios and venting in gas furnaces, and refrigerant charge in DX air conditioners and heat pumps.
In order to deliver rated capacities from heating and/or cooling equipment, airflow must be correct. Either too much or too little airflow will keep equipment from operating efficiently at design capacity. Essentially, there is a sweet spot at which high efficiency occurs.
Older Lower Efficiency Equipment
Figure 1 illustrates this ‘sweet spot’ in the form of a bell curve with the y-axis representing efficiency, and the x-axis representing airflow. Older, less efficient equipment has a fairly wide ‘sweet spot.’
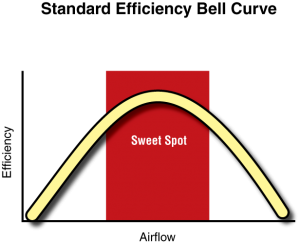
Figure 1. Performance in older equipment.
What this means is there is a fair amount of forgiveness with 70 to 80% furnaces and 8 to 12 SEER equipment.
On older DX systems, analog gauges were good enough to measure things like superheat and subcooling. On older fossil fuel equipment, there is much more forgiveness in terms of gas pressures and oxygen, as long as CO levels are under 100 ppm and stable.
In other words, on older systems, we had a lot more leeway within that sweet spot. This is not the case with newer, high-efficiency equipment.
High-Efficiency Equipment
Figure 2 illustrates the bell curve and sweet spot on today’s high-efficiency heating and cooling equipment. To achieve higher ratings, this equipment must work within a much tighter range. This means airflow needs to be dialed in much more accurately.
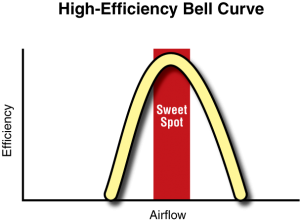
Figure 2. Performance in newer high-efficiency equipment.
On DX systems, the refrigerant charge must also be very precise, either weighed in properly or by hitting exact subcooling and superheat numbers using digital gauges. Precise charge for maximum efficiency can only be achieved when there is proper airflow through the system.
Variable Refrigerant Flow DX systems are somewhat more forgiving when it comes to airflow, but even these systems will never reach their design capacities and efficiencies without proper airflow. The same applies to newer high-efficiency furnaces.
These bell curves are not designed to be precise efficiency curves for every system, rather they are meant to illustrate the differences between older equipment and their newer counterparts.
Are your field people using state-of-the-art digital test instruments and modern testing methods to test and adjust today’s more ‘sensitive’ equipment? Learn to hit the sweet spot on your installations, and give your customer the comfort and efficiency they deserve.
Recent Comments