Yes, I’m talking about the bay doors on the loading dock. Each of the four 25-ton and the 70-ton units were set to operate ±10%. However, they were not reducing the heat load as they were designed. The humidity and temperature were still high in the server area.
Several weeks later the general manager of the server farm wanted to meet and go over the TAB report. He said they planned to add another 50-tons of cooling and two more 65,000 CFM exhaust fans. However, they couldn’t do any of this work without upgrading the transformer.
They had a request in to the landlord but had to wait to have the transformer changed out. The GM then wanted testing and balancing done on this additional equipment.
From Bad to Worse
Unfortunately, the landlord said they could not increase the transformer size. That meant the server farm owners needed to buy or rent generators to operate the new RTUs and exhaust fans.
I didn’t believe this would work, but the customer is always right. They had the equipment installed and started it up. Here is what then happened:
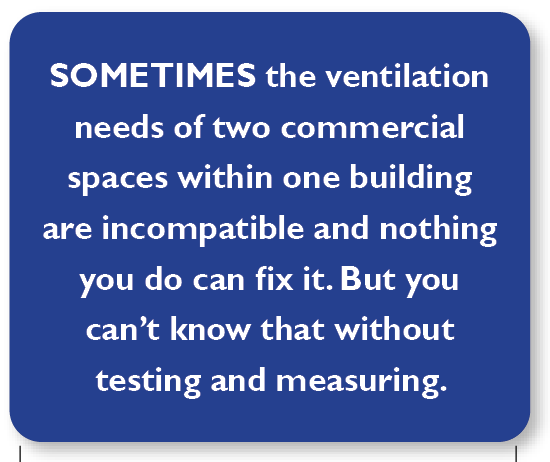
After they installed these units and fans, they had 220 tons of cooling (88,000 CFM) on an 85,000 sq. ft. building. However, there was no outside air coming through the units.
Now they had five 65,000 CFM exhaust fans providing 325,000 CFM total exhaust. The fans were not used constantly. Walking around the facility was like walking inside a vacuum cleaner in some places and a hurricane in others. The units were set and operating ±10%.
The dry bulb ranged from 75 to 85F, however, the humidity was between 45 to 55%. The smell from the brewery was worse after adding the equipment. This was with the exhaust fans running. We had no way to resolve the smell from the brewery coming through the wall.
While working on the server farm, we spoke with the new owners of the brewery next door, to see if they were still having issues with their equipment. They were and didn’t know why. I explained to them all the pressurization issues their neighbor was having and that most likely was causing their problems.
Ultimately, the server farm owners decided to relocate this facility and moved out. Soon after, we received a call from the microbrewery and asked to come back and retest their side of the building.
Finally, Good News
After retesting and measuring the microbrewery, we found their static pressures changed from .15-in. negative to .03-in. positive. We had access to the old server farm, so I went in there to see if you could still smell beer. The smell was still lingering but didn’t seem to be coming through the wall.
Here is what we discovered: The ventilation needs of these two spaces were incompatible. The firewall was not suited as a good barrier between them. When the fans on the server-side of the building came on, the amount of outside air was overwhelming. The additional outside air coming from the back of the building also added to the imbalance.
We still talk about this project. I still wonder how air can be pulled through something like a firewall. That doesn’t make sense. Nevertheless, the brewery came full circle, and this became the “best worst” job we ever worked on.
Unfortunately, in 2020 the brewery went out of business due to Covid.
The lesson learned from this experience is that even though pressure testing a building may seem unorthodox, it can save your customer big money and eliminate many headaches for them and for you.
Darl Works is president of Performance Air Balancing, Inc., a 16-year-old Testing, Adjusting, and Balancing (TAB) firm based in Crystal River, FL. He is a National Balancing Council (NBC) Qualified Supervisor who oversees the daily operations and performs TAB report review and certification. He can be reached at ncilink.com/ContactMe.
Ryan
I agree with your comment. I was told, this is how they operate their cloud farm. Bring in unconditioned air, attempt to condition it, then exhaust the air out of the building.
Isn’t the exhaust fans for the server fan rather counter intuitive? Why didn’t they add more RTU’s for additional heat??