Can a neighbor affect your building pressure when you are only separated by a two-hour firewall? The short answer is “YES”!
Remember, the truth can be stranger than fiction and commercial buildings need our help.
Here’s the story: A few years ago, we were called out to a microbrewery experiencing a building pressure issue. The client explained that after the tenant moved in next door, the brewery was having issues with its equipment. The biggest issue was with a cooker used to brew beer.
So we conducted an onsite survey of the building and equipment and everything seemed to be in working order. We also inspected the firewall between the brewery and their tenant and found no issues there, either.
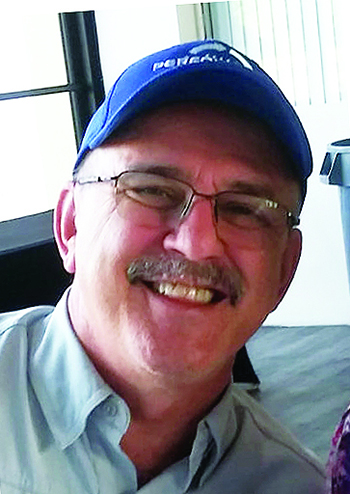
The microbrewery had 30 tons of cooling and one 12-foot kitchen hood with makeup air. There were different types of brewery processing equipment using either exhaust or makeup air or a combination of both. We tested out all the equipment. Everything was working fine. We could not find anything wrong with the brewery’s cooling units. This was not the outcome anyone wanted.
A few weeks later we received another call from the brewery. A power-exhaust burner back-drafted and caused the control wiring to melt. I made a trip out to see what was going on and again, had no more success than before.
I placed Data loggers on-site for seven days and once again found no major issues.
This was driving all of us crazy. After nearly four months, we couldn’t recreate what was going on.
The Next Door Neighbor
Six months later we received a call from an Atlanta-based company that needed a functional performance test done on their equipment in their Tampa server facility. They said the electric company was having an issue with the amount of power they were using.
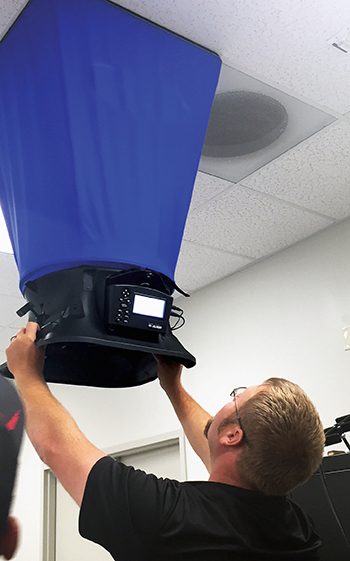
When I pulled into the parking, I saw that our brewery client was next door! How is that for a small world!
We walked through the server farm facility and got to the area next to the brewery. You could smell beer coming through the firewall. That is when it dawned on me that the server farm was somehow the culprit of the issues at the microbrewery.
The server farm used three 65,000 CFM exhaust fans, four 25-ton and one 70-ton rooftop units (RTUs). They planned to install three more fans on the loading dock. The client said they operated the RTUs 24/7. However, the fans were designed to operate only when it was necessary to remove excess heat.
Next Steps
To tackle this unique situation, we took it one unit at a time, traversing with a pitot tube, and vel-grid. When we finished our testing, we could still smell the brewery through the firewall.
By the way, the firewall is a 6-in. frame with fire-resistant insulation and two layers of 5/8-in. fire-rated sheetrock on both sides. At the front door of the server farm, the pressure was at 0.21 in. with all the fans and RTUs operating.
The dry bulb in the server farm space ranged between 80 to 85F. The humidity ranged from 55 to 60%. The space was around 85,000 sq. ft., and the building was built in the early 1980s. After performing our testing, adjusting, and balancing measurements (TAB), we told them they needed additional make-up air. The server farm general manager decided to use the bay doors as make-up air for the back part of the building!
Click Below for the Next Page:
Ryan
I agree with your comment. I was told, this is how they operate their cloud farm. Bring in unconditioned air, attempt to condition it, then exhaust the air out of the building.
Isn’t the exhaust fans for the server fan rather counter intuitive? Why didn’t they add more RTU’s for additional heat??