The customer didn’t understand what replacing the TXV meant and decided to get a second opinion. They called a company their daughter was familiar with. That company sent one of its technicians, who was also NCI certified, and they discovered that the ductwork was a contributing factor to the high superheat issue during operation.
A “No Silver bullets” Case Study
Upon arrival, I found that the technician had already pumped down the system and replaced the TXV. After evacuating the system and recharging it with refrigerant, the technician started the system and allowed it to stabilize. He was confident it was ready to test.
After running for about 10 minutes, we found the problem still existed. That instantly, shattered the tech’s confidence.
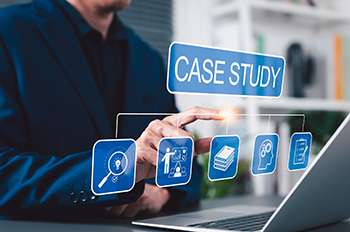
Fortunately, he replaced the TXV with an adjustable version and a tee on the outlet of the evaporator coil. This allowed us to see the operating superheat and make slight adjustments to tune it to the manufacturer’s specifications.
The tech never adjusted a TXV before because he was wrongly taught that you didn’t need to adjust or couldn’t adjust them. Note: there are non-adjustable TXVs, it may be wise not to use them.
After adjusting the TXV, we returned to the diagnostic forms and completed the temperature measurements necessary to calculate the target suction and liquid line temperatures. We then compared them to the actual temps of the line sets, and that is when we discovered the underlying issue.
Discovering the Real Problem
During the original installation, the line sets were not piped through the attic. Instead, they were installed under the concrete foundation, which is not a bad thing unless you encounter what we found.
The line set temperature changes, according to industry standards, shouldn’t be greater than five degrees. Our measurements showed a 14 to 16-degree temperature increase in the suction line, which would make it impossible to control compressor superheat.
This issue raised several more questions, including:
- Is there a slab leak
- Is this issue being caused by the sprinklers?
Whatever the cause, it was obvious that the line set needed to be relocated and properly insulated, started up, and tested. I witnessed that tech’s confidence return by doing these things. Plus it set the homeowner to consider the stage for the second tech’s findings .
Ultimately, the homeowner had the first company relocate and replace the line set. Since the ductwork was old and showing signs of age, the homeowner had the second company replace it. The job turned out better than expected, and both companies used it as a learning experience.
The bottom line is that state and federal codes are NOT the basis of comfort excellence. They are minimum standards. It truly requires training, certification, and practice to effectively integrate testing and measurement into your service and installation teams. Again, there are no silver bullets.
These procedures and processes are all part of what we call the High-Performance HVAC approach, which prioritizes the customer’s comfort, energy efficiency, and health needs.
Oh, and in the case of our above-mentioned case study, teamwork to solve invisible problems that make customers very happy also builds confidence in your techs and ultimately leads to profitable work.
Jeff Sturgeon is the Southern California Training Center Manager/Instructor for National Comfort Institute (NCI). He has over 40 years of experience in residential and commercial HVAC and refrigeration fields. Jeff works with hundreds of contractors and their field personnel to help ensure the successful implementation of Southern California Edison’s Workforce Education and Training programs. Contact him at ncilink.com/ContactMe.
Recent Comments