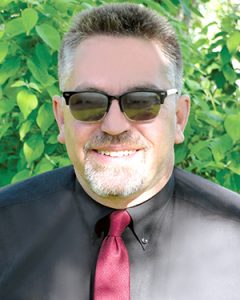
Scott Fielder, Director of Field Operations for Evergreen Telemetry
When I first began my career in hydronic testing, adjusting, and balancing (TAB), I asked why so few people knew how to ‘water balance’ relative to the number of people doing air balancing. My employer told me he didn’t know. He learned to perform both air and water balancing at the same time, and he expected me to do the same. There was no great mystery to it. It was fluid moving through metal and the same laws of physics applied. In other words, you balance a hydronic system with the same methodology used to balance grilles.
Then two hours into my very second day, I closed the wrong valve and crashed a $250,000 chiller at Dallas-Fort Worth (DFW) Airport. The facilities manager put his arm around me and said, ‘I sure hope you’re the owner’s son or something, because if that chiller doesn’t come back on line, you’ll probably be looking for a new job.’
The point being, that a TAB technician has to go out of his or her way to damage a system when performing air balancing. Whether it’s drilling into a coil when they should have looked first, or tossing a Variable Frequency Drive into Hand (Manual Operation) and blowing the ductwork apart, it takes some effort to cause harm to an air system. It only takes a simple mistake to cause tens of thousands of dollars of damage to a hydronic system.
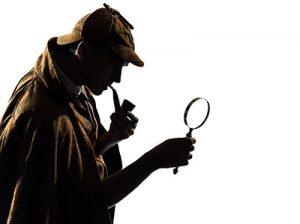
Many people are mystified by Hydronics rules, but in fact, it’s just a TAB guy behind the curtain with a different meter. Losing the fear of hydronic TAB is the key component taking advantage of this tremendous opportunity.
Hydronic TAB: Nothing to Fear
In spite of this danger there is nothing to fear, provided you take a cautious and educated approach.
Here are three steps that should help tremendously:
First, don’t hire people who aren’t mathematically proficient. Why? There are calculations involved when doing testing, adjusting, and balancing. For those who aren’t proficient or aren’t willing to become more proficient, his or her mistakes can be costly. So hire right. The financial penalties for hiring wrong are severe in hydronic TAB.
The second step is to educate yourself. Companies such as Grundfos, Flow Design/IMI, Taco, and Bell & Gossett have some fantastic articles and training modules free online. There are also some great books out there, such as ‘The Pump Handbook,’ by Karassik, Krutzsch & others as well as ‘Pumping Away,’ by Holohan. It’s stated that the best professionals in any field read at least 15 minutes a day in their given field. I’m a strong proponent of this philosophy, as are some of the great names in our trade.
The third and most pragmatic step is to teach hydronics to your technicians at the same time you’re teaching them air balancing. As you balance grilles, remind them that the same principles apply to balancing coils or circuit setters. When you apply fan laws — for example — when sizing a sheave, be sure to point out that they are the same as the pump laws. CFM and PD decrease and increase on a one-to-one ratio. GPM and Impeller Diameter decrease and increase on a one-to-one ratio. As CFM increases, Amps increase by a cubed ratio. As GPM increases, Amps increase on a cubed ratio.
It’s Just Physics …
It’s physics. We balance fluid moving through metal by adjusting mechanical devices. For air systems, we adjust dampers. In hydronic systems, we adjust valves and circuit setters.
In closing, there are tremendous opportunities when you decide to expand into hydronic testing, adjusting and balancing. Many people believe there is great and powerful magic dictating the rules, but in fact, it’s just a TAB guy behind the curtain with a different meter. Losing the fear of hydronic TAB is the key component to entering this strange new world. Just remember to proceed cautiously.
As a foot note, that chiller in Dallas 20 years ago — it came back on line. I probably wouldn’t be typing this if it had not.
Nice article Scott! Good reading.