At this time, my company drained the heating system and removed the large cast iron radiators. The project scope included installing new heating pipes under the sub-floor and routing them to the new cast iron baseboards.
I analyzed the plans and noticed that the specified cast iron baseboards were alarmingly short, mainly because the plan was not to open the exterior walls and insulate them.
To verify that the heat loss and emitter sizing were correct, I ran a Manual J load calculation and modeled the home with the “As-is” exterior wall assemblies.
I found that the cast iron baseboards were extremely undersized—most by half of the required length.
Solutions and Problems
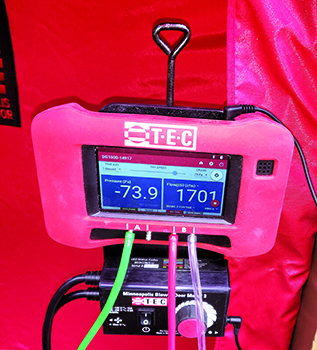
the home using a blower door test.
In the face of this challenge, we devised an innovative solution. We proposed using closed-cell foam to reduce the heat requirements, a decision that led to the removal of the plaster on the exterior walls for insulation.
However, Donovan thought preserving the original walls in one of the bedrooms was essential to maintaining a crucial part of the home’s history.
With the second floor now insulated, we could reduce the heating requirements, effectively reducing the required length of the cast iron baseboards throughout.
We seamlessly integrated these baseboards into custom cabinetry in each room, a testament to the team’s creativity and problem-solving skills. Heating a home without seeing or hearing the system is truly magical.
The solution also became a big problem. By insulating the exterior wall, we reduced the heat loss of the second floor, but the foam also reduced the heat gain.
This means that the existing heat pump and air handler (used for cooling) were now oversized. The ground source heat pump was a two-stage, three-ton unit. After running a load calculation, we determined that a two-ton, two-stage unit would be the correct sizing for the new load.
Revisit the Unico System
We also scrutinized the existing Unico duct design. We could delete a handful of supply ducts from the second floor since we were now installing a smaller-sized heat pump. I replaced the existing 16 x 25 x 4-in. media air cleaner with an Aprilaire model 1210. The 1210 is Aprilaire’s 20 x 25 x 4-in. model.
Although we didn’t need the larger filter as a means to reduce the pressure drop, I wanted to take advantage of being able to reduce the filter face velocity. By doing so, we increased the filter’s efficiency and effective duty cycle, allowing more time for loading.
Two days before scheduling the drywall installation, Donovan noticed the snow slightly melting in two spots on the roof’s front side of the home. The walls of the third floor are angled because they are part of the roof assembly. The rafter cavities are inaccessible since the third floor is finished and dry-walled.
The roof assembly is second to none, very similar to the recommendations made by Joseph Lstiburek, founder of the Building Science Corporation. He is considered one of the godfathers of building science. To prevent thermal bridging, Joe recommends adding a layer of 2-in. foam on top of the plywood roof deck. He then suggests adding wood sleeper strips and then another layer of plywood on top of the sleepers.
This method provides insulation below the rafters with the closed cell foam and above them with the 2-in. foam board. This construction method also provides an air gap, which acts as a mini channel for air to cool the shingles in the summer.
Click Below for the Next Page:
Recent Comments